Flexible Thin-Film Electronics
Alessandro Volta created the first electrical circuit in 1800 using salt-water solutions connected by pieces of metal. Volta went on to invent many electronic systems, most notably the Voltaic Pile (the first battery). [1] Fast-forward and electronics are ubiquitous throughout our lives. Most electronic devices are composed of rigid circuit boards containing electronic components (e.g., transistors, resistors, and capacitors), and printed metallic interconnects. Now, flexible electronics are currently being developed for next-generation devices. Flexible electronics can be used for an incomprehensible number of applications, [2] but some include, foldable displays, conformal photovoltaics, batteries, power generators, wearable sensors, soft robotics, and bioelectronic interface applications. [3, 4]
1. Flexible Metalic Thin-film Conductors
Flexible electronics require patterned conducting materials that can withstand strain without losing conductivity to enable functionality for a variety of applications. To achieve conducting pathways, or interconnects, different materials can be used including but not limited to conducting polymers (e.g., PEDOT:PSS), [5, 6] carbon materials (e.g., graphene, CNTs), [7, 8] oxides (e.g., ITO), [9] liquid metal (e.g., EGaIn), [10, 11] metal nanowires,[12] and metallic thin films. [13–16]
Often, to achieve conducting structures, small islands of rigid electronics are assembled on to a flexible polymer substrate and connected using thin-film metallic interconnects or electrodes. The mechanical properties of the metal layers and their adhesion to the flexible substrate, especially during strain, are of the utmost importance to their functionality. The failure of these layers is either via i) fracture through the thickness of the layer or ii) the metallic layers delaminate from the substrate. [16] Thus the study of metallic interconnects and their failure during strain or bending is imperative to develop flexible electronic devices.
The through-thickness fracture of metallic interconnects can be studied by tensile strain testing and bending experiments. The deformation of metallic thin films on flexible substrates has been examined by tensile testing and monitoring the effects by X-ray diffraction and microscopy. [17] [18] For example, Gruber et al. studied the cracking behavior of copper (Cu) films on polyimide (PI) with tantalum (Ta) interlayers. The fracture toughness of the Cu films increases with Cu film thickness and decreases with increasing Ta interlayer thickness. When the Cu films were thinner than 70 nm, they exhibited inherent brittle fracture.
Furthermore, the mechanical failure of brittle, thin films on a flexible substrate, when bending, can be observed by optical microscopy. Glushko et al. demonstrated the variable mechanical cracking of printed silver (Ag) interconnects via cyclic tensile, compressive, and mixed tensile compressive bending strains. Conversely, evaporated Ag thin films showed no fracture dependence on the type of strain. [19]
The adhesion of metallic thin film interconnects to the flexible substrate is also critical to their performance. [16] Gold (Au) or Ag are ideal materials for interconnects because they are ductile, have a low electric resistance, and can be easily deposited and patterned. However, these metals sometimes delaminate from flexible polymer substrates. The delamination typically manifests as buckling from the substrate. Therefore, titanium (Ti), tantalum (Ta), or chromium (Cr) interlayers are used to improve the adhesion of metallic thin films to the polymer substrate. Confocal laser scanning microscopy (CLSM) can be used as a tool to measure the buckling of metallic thin films during compression-induced delamination.
As shown in the digest article “Thin Film Adhesion of Flexible Electronics Influenced by Interlayers,” the adhesion properties of Au and Au/ Ta thin films on PI, under compressive strain, was investigated. [16] CLSM was used to measure the buckling dimensions under compressive strain. The dimensions of the buckles can be used to calculate the critical buckling and driving stresses, using the Hutchinson and Suo model. The studies show that Au thin films spontaneously buckle, while a compressive strain is required to delaminate the Au/Ta film, indicating larger adhesion energy.
Further Reading:
https://onlinelibrary.wiley.com/doi/ abs/10.1002/admt.201700277
https://onlinelibrary.wiley.com/ doi/10.1002/aenm.201700535
Appl. Note: https://www.olympus-ims.com/en/applications/electro-mechanical_behavior_of_thin_films/
Appl. Note: https://www.olympus-ims.com/en/applications/quantitative_investigations_of_the_interconnect/
2. Conductive Polymer Membranes
Flexible electronics can be used for wearable devices for applications such as movement sensors, biological sensors, triboelectric nanogenerators, flexible power supplies, and actuators. [20] Obtaining flexible conductors that can withstand high strain and has low resistance is a challenge in the fabrication of flexible electronic devices. Moreover, an additional requirement for wearable electronics, especially those in contact with skin, is that they have relatively high porosity compared to more established flexible electronics. This is because the comfort of wearable devices is contingent on air permeability. Attaining flexibility, elasticity, high conductivity, high mechanical integrity, and porosity is an active research area. [12]
Flexible electrodes are generally composed of an elastic substrate as the elastomer to support bending, stretching, and twisting. However, these materials are nonporous and do not provide breathability. One solution to the lack of air permeability of flexible electronics is to prepare conductive polymer membranes. Conductive polymer membranes are composed of a network of stretchable polymer fibers and conductive additives. The network of polymer fibers is inherently porous and allows for gas permeability. Methods of fabrication include the inclusion of conductive additives into yarns, fabrics, and breathable ionic membranes, [21] coating of textiles, [22] using cellulosic templates, electrospraying, [22] electro‐hydrodynamic direct‐writing, [23] and electrospinning polymer fibers. [12, 24]
In the article digest “Breathable and Flexible Polymer Membranes with Mechanoresponsive Electric Resistance,” [12] the authors demonstrate a flexible, highly conductive membrane with inherent porosity to allow for gas permeability. The membrane was fabricated by first electrospinning polyurethane (PU) to form polymer nanofiber mats. Conductive Ag nanowires (AgNWs) are dispersed onto a membrane via a filtration method.
Finally, a sandwich is made with the AgNWcoated PU membrane and another PU membrane. Polycaprolactone fibers were used to improve the adhesion of the sandwich. The resulting membranes had a low sheet resistance, showed excellent stability to mechanical strain, and allowed gas permeation.
Further Reading:
https://onlinelibrary.wiley.com/doi/ abs/10.1002/adma.201908496
3. Flexible Micropillar Electrode Arrays
Flexible electronics have also shown promise in bioelectronic interface applications. Bioelectronic electrodes are essential to investigate the relationship between electricity and biology (electrophysiology). [25, 26] Bioelectronic electrodes can be utilized for both bioimpedance and biopotential measurements. Forming intimate interfaces between electrodes and biological matter (e.g., neural tissue) are important to achieve high fidelity biological to electrical signal transduction. [26]
For example, neural electrode techniques have considerably improved our ability to understand brain function and have become a tool for the clinical diagnosis and treatment of neurological disorders. Creating tight interfaces, and good electrical contact, between conventional subdural electrodes and neural tissues, is challenging due to their large mechanical mismatch. Thus, flexible electronics are well suited for neural electrode applications. Fabrication of flexible bioelectronics typically uses metal evaporation, atomic layer deposition, photolithography, and transfer printing, and inkjet printing. [25, 27] Nonetheless, conventional flexible substrates such as PI and polydimethylsiloxane (PDMS) still have moduli much higher than neural tissue. [26]
To address this issue, Du et al. prepared novel flexible micropillar electrode arrays (μPEAs) based on a biotemplate method, which is described in the article digest “Flexible Micropillar Electrode Arrays for In Vivo Neural Activity Recordings.” [26] The μPEAs were prepared by using a lotus leaf to create a template that was filled with a flexible material and coated in Au for conductivity. Each electrode contained many hierarchical micropillars, which contained surface nano-scale wrinkles (Figure 1). The μPEAs were engulfed by the neural tissue, forming a low impedance interface, which allows for in vivo multichannel recordings with a high signal-to-noise ratio.
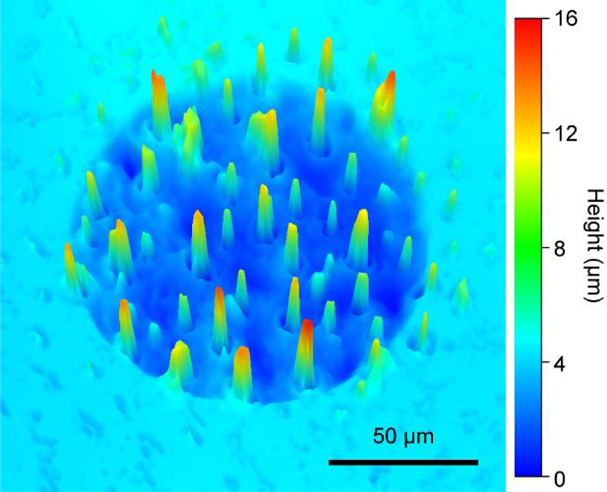
References
[1] A Short History of Circuits and Systems, in: F. Maloberti, A.C. Davies (Eds.), 2016.
[2] A. Nathan, A. Ahnood, M.T. Cole, S. Lee, Y. Suzuki, P. Hiralal, F. Bonaccorso, T. Hasan, L. Garcia-Gancedo, A. Dyadyusha, Flexible electronics: the next ubiquitous platform, Proc. IEEE, 2012, 100 1486–1517.
[3] S. Huang, Y. Liu, Y. Zhao, Z. Ren, C.F. Guo, Flexible electronics: stretchable electrodes and their future, Adv. Funct. Mater., 2019, 29 1805924.
[4] H. Ling, S. Liu, Z. Zheng, F. Yan, Organic flexible electronics, Small Methods, 2018, 2 1800070.
[5] X. Fan, W. Nie, H. Tsai, N. Wang, H. Huang, Y. Cheng, R. Wen, L. Ma, F. Yan, Y. Xia, PEDOT: PSS for flexible and stretchable electronics: modifications, strategies, and applications, Adv. Sci., 2019, 6 1900813.
[6] W. Dang, V. Vinciguerra, L. Lorenzelli, R. Dahiya, Printable stretchable interconnects, Flex. Print. Electron., 2017, 2 013003.
[7] B.K. Sharma, T. Das, J.-H. Ahn, Graphene for Flexible Electronics, Flexible Carbon-based Electronics, 2018, 95–130.
[8] Y.Y. Chen, Y. Sun, Q.B. Zhu, B.W. Wang, X. Yan, S. Qiu, Q.W. Li, P.X. Hou, C. Liu, D.M. Sun, High-Throughput Fabrication of Flexible and Transparent All-Carbon Nanotube Electronics, Adv. Sci., 2018, 5 1700965.
[9] V. Zardetto, T.M. Brown, A. Reale, A. Di Carlo, Substrates for flexible electronics: A practical investigation on the electrical, film flexibility, optical, temperature, and solvent resistance properties, J. Polym. Sci. B: Polym. Phys., 2011, 49 638–648.
[10] R. Guo, B. Cui, X. Zhao, M. Duan, X. Sun, R. Zhao, L. Sheng, J. Liu, J. Lu, Cu–EGaIn enabled stretchable e-skin for interactive electronics and CT assistant localization, Mater. Horiz., 2020.
[11] M.g. Kim, C. Kim, H. Alrowais, O. Brand, Multiscale and Uniform Liquid Metal Thin-Film Patterning Based on Soft Lithography for 3D Heterogeneous Integrated Soft Microsystems: Additive Stamping and Subtractive Reverse Stamping, Adv. Mater. Technol., 2018, 3 1800061.
[12] Q. Gao, B.A. Kopera, J. Zhu, X. Liao, C. Gao, M. Retsch, S. Agarwal, A. Greiner, Breathable and Flexible Polymer Membranes with Mechanoresponsive Electric Resistance, Adv. Funct. Mater., 2020, 1907555.
[13] P. Heremans, A.K. Tripathi, A. de Jamblinne de Meux, E.C. Smits, B. Hou, G. Pourtois, G.H. Gelinck, Mechanical and electronic properties of thin-film transistors on plastic, and their integration in flexible electronic applications, Adv. Mater., 2016, 28 4266–4282.
[14] A. Martin, B.S. Chang, Z. Martin, D. Paramanik, C. Frankiewicz, S. Kundu, I.D. Tevis, M. Thuo, Heat-Free Fabrication of Metallic Interconnects for Flexible/Wearable Devices, Adv. Funct. Mater., 2019, 29 1903687.
[15] S.P. Lacour, J. Jones, Z. Suo, S. Wag- ner, Design and performance of thin metal film interconnects for skin-like electronic circuits, IEEE Electron Device Lett., 2004, 25 179–181.
[16] A. Kleinbichler, M. Bartosik, B. Völker, M.J. Cordill, Thin Film Adhesion of Flexible Electronics Influenced by Interlayers, Adv. Eng. Mater., 2017, 19 1600665.
[17] S. Olliges, P.A. Gruber, V. Auzelyte, Y. Ekinci, H.H. Solak, R. Spolenak, Tensile strength of gold nanointerconnects without the influence of strain gradients, Acta Mater., 2007, 55 5201–5210.
[18] P.A. Gruber, E. Arzt, R. Spolenak, Brittle-to-ductile transition in ultrathin Ta/Cu film systems, J. Mater. Res., 2009, 24 1906–1918.
[19] O. Glushko, M.J. Cordill, A. Klug, E.J. List-Kratochvil, The effect of bending loading conditions on the reliability of inkjet printed and evaporated silver metallization on polymer substrates, Microelectron. Reliab., 2016, 56 109–113.
[20] W. Zeng, L. Shu, Q. Li, S. Chen, F. Wang, X.M. Tao, Fiber-based wearable electronics: a review of materials, fabrication, devices, and applications, Adv Mater, 2014, 26 5310–5336.
[21] A. Gugliuzza, E. Drioli, A review on membrane engineering for innovation in wearable fabrics and protective textiles, J. Membr. Sci., 2013, 446 350–375.
[22] Q. Qiu, M. Zhu, Z. Li, K. Qiu, X. Liu, J. Yu, B. Ding, Highly flexible, breathable, tailorable and washable power generation fabrics for wearable electronics, Nano Energy, 2019, 58 750–758.
[23] D. Ye, Y. Ding, Y. Duan, J. Su, Z. Yin, Y.A. Huang, Large-Scale Direct-Writing of Aligned Nanofibers for Flexible Electronics, Small, 2018, 14 1703521.
[24] C. Wang, K. Xia, H. Wang, X. Liang, Z. Yin, Y. Zhang, Advanced carbon for flexible and wearable electronics, Adv. Mater., 2019, 31 1801072.
[25] Y. Khan, F.J. Pavinatto, M.C. Lin, A. Liao, S.L. Swisher, K. Mann, V. Subramanian, M.M. Maharbiz, A.C. Arias, Inkjet-printed flexible gold electrode arrays for bioelectronic interfaces, Adv. Funct. Mater., 2016, 26 1004–1013.
[26] M. Du, S. Guan, L. Gao, S. Lv, S. Yang, J. Shi, J. Wang, H. Li, Y. Fang, Flexible Micropillar Electrode Arrays for In Vivo Neural Activity Recordings, Small, 2019, 15 1900582.
[27] A. Carlson, A.M. Bowen, Y. Huang, R.G. Nuzzo, J.A. Rogers, Transfer printing techniques for materials assembly and micro/nanodevice fabrication, Adv. Mater., 2012, 24 5284–5318.
Source: DOI: 10.1002/smll.201900582; M. Du, S. Guan, L. Gao, S. Lv, S. Yang, J. Shi, J. Wang, H. Li, and Y. Fang; small; © 2019 WILEY-VCH Verlag GmbH & Co. KGaA, Weinheim