Super-Hydrophobic and Oleophobic Aluminum Alloy Surfaces via Chemical Etching and Functionalization
Super-hydrophobic and oleophobic surfaces on ASTM 1200 H14 aluminum alloy substrates were achieved by chemical etching followed by the deposition of organically modified silicate coatings. The chemical etching solutions iron(III) chloride + hydrogen chlorine + hydrogen peroxide and etching time were varied to increase the surface roughness. The chemical etching produces rough surfaces with superficial square pores and edges about 1 μm–2 μm. The chemical modifications modified silicate solutions based on perfluorooctyltriethoxysilane (PFOTES) and hexadecyltrimethoxysilane (HDTMS) sol-gel precursors induced water contact angles about 154° and 150°, respectively. Moreover, the surface modification based on PFOTES demonstrated an oleophobic character with an oil contact angle of 136° due to air entrapment in the surface roughness at the oil-aluminum interface.
Introduction
In the last decades, the development of super-hydrophobic surfaces has received attention due to their interesting properties and potential applications on the surface of metals, ceramics, and polymers. [1–12] Such surfaces exhibit almost no interaction with water, showing contact angles higher than 150°. [13] Some benefits of super-hydrophobic surfaces include easy cleaning, anti-adherence, and corrosion resistance. [4,13] Thus, the production of surfaces with such properties on aluminum alloys has attracted particular interest due to the many potential applications of such a light metallic substrate, especially to increase corrosion protection. [14] Further, the control over the wettability of organic and apolar fluids such as oil, is also sought for many applications. [4,15,16] In this context, various studies have been carried out to create surfaces that are both super-hydrophobic and super-oleophobic. Such surfaces, called super-amphiphobics, can repel both water and oil. [17–19] These surfaces are commonly prepared by increasing surface roughness and reducing surface energy. [8,20–23]
Several techniques create rough superficial structures on metals, including chemical etching, anodic oxidation, lithography, and deposition of nanoparticles. [18,24,25] Chemical etching, accelerated and controlled corrosion, [26] is commonly used because it is an easy and cheap method. [18] Aqueous solutions of iron (III) chloride (FeCl3) have been used in industry as a chemical etching agent [27] for metals such as steel, aluminum, and copper alloys. [26] As an example, Liu et al. [1] produced superhydrophobic surfaces in AISI 304 stainless steel by creating a micro-/nanostructure, using an etching solution composed of FeCl3 + HCl + H2O2 (FHH), followed by a coating deposition using the dodecyltriethoxysilane precursor. We applied this method to create a rough surface on an aluminum substrate for the first time.
Organically modified silicates (ORMOSIL) are organic-inorganic hybrid materials synthesized by hydrolysis and condensation reactions of organically modified silanes precursors. [28] The most straightforward class is formed from precursors with chemical formula as RSi(OCH3)3, where R is an organic terminal group that does not create bridges in the three-dimensional gel network. [29] In the case of hexadecyltrimethoxysilane (HDTMS) and 1H,1H,2H,2H-perfluorooctyltriethoxysilane (PFOTES) precursors, the R groups are composed of C–H and C–F bonds, respectively; they are responsible for the hydrophobic and oleophobic character of the functionalized materials.
Herein the surface of ASTM 1200 H14 aluminum alloy was chemically and morphologically modified with an etching treatment in the FHH solution [1] followed by the deposition of hybrid organic-inorganic coatings based on modified silica materials obtained by sol-gel process. PFOTES and HDTMS were used as alkoxide precursors to obtain the super-hydrophobic surface. The surface morphology was characterized by confocal microscopy, and contact angle measurements with deionized water and mineral oil were carried out to characterize the modified aluminum alloy surfaces' functionality.
Methods
The ASTM 1200 H14 aluminum alloy sheets with a size of 60 mm × 40 mm × 0.3 mm (2.36 in. × 1.57 in. × 0.01 in.) were cleaned with acetone and deionized water in an ultrasonic bath for 5 minutes each. After cleaning, the samples were immersed in an FHH solution consisting of a mixture of iron (III) chloride aqueous solution with concentrations ranging from 0.05 mol L-1 to 0.50 mol L-1, 37% hydrochloric acid, and 35% hydrogen peroxide with volume proportion of 10:1:1, respectively. [1] The immersion times were 5, 7, 10, and 15 minutes. After etching, the samples were cleaned using a soft sponge, rinsed with deionized water, and washed with acetone and deionized water in an ultrasonic bath for 5 minutes. Then, water was removed with a hot air flow followed by drying in an oven for 20 minutes at 60 °C (140 °F).
ORMOSIL sol-gel solutions were prepared by hydrolysis and condensation of the hybrid precursors PFOTES and HDTMS in the presence of ethanol, deionized water, and 37% HCl. The molar ratio Precursor:EtOH:H2O:HCl was kept at 1:856:7.2:0.9. Coatings using TEOS and mixtures of TEOS with PFOTES as sol-gel precursors with the same molar proportions were also performed for comparison. Then, the solgel solutions were vigorously stirred for 2 minutes. The deposition was performed at room temperature using dip-coating. The deposited coatings were then heat-treated in an oven for 30 minutes at 60 °C (140 °F). Then, the oven temperature was raised to 120 °C (248 °F) for another 60 minutes. The chemical etching, followed by the deposition process of the ORMOSIL coating, is schematized in Figure 1.
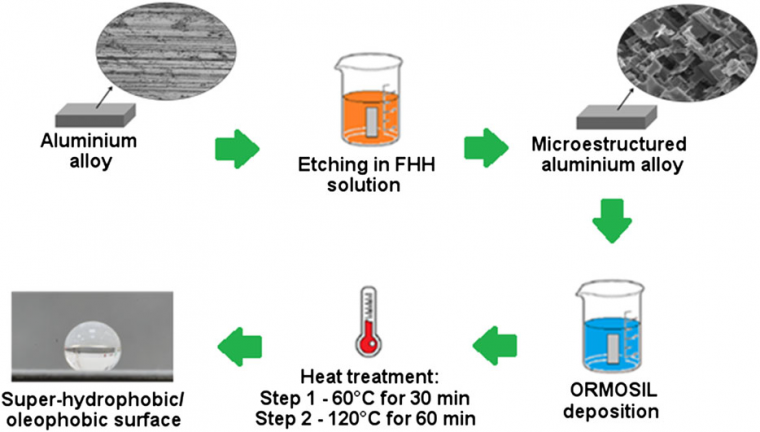
The samples' surface morphology and roughness measurements were evaluated using a confocal microscope (Olympus LEXT OLS4100 3D laser confocal microscope). For the roughness measurements, a cut-off value of 80 μm and a Gaussian filter were selected. The chosen analysis parameter to quantify the roughness was the average roughness (Ra) determined from a cross-sectional line of 180 μm in length drawn along the surface samples.
The coating hydrophobicity and oleophobicity were quantified by water and oil contact angle (WCA and OCA) measurements using ~ 10 μL of deionized water and ~5 μL mineral oil, respectively. A portable optic tensiometer was used for the measurements.
Results and Discussion
The FeCl3 concentration of the FHH etching solution and the time of immersion was varied to optimize the aluminum substrates' roughness. Images obtained by confocal microscopy and the corresponding roughness values of the samples etched for 5 min in FHH solution with FeCl3 concentrations of 0.05 mol L-1, 0.1 mol L-1, 0.25 mol L-1, and 0.5 mol L-1 are presented in Figure 2. The as-received aluminum has a roughness Ra = 0.21 μm. The 0.05 mol L-1 FeCl3 solution was not sufficient to create a uniformly rough surface, leading to a partial etching and Ra = 0.7 μm. For FeCl3 concentrations of 0.1 mol L-1 and 0.25 mol L-1, irregular and porous microstructures were uniformly formed over the entire surface, presenting higher Ra = 1.29 μm and Ra = 1.27 μm, respectively. The FeCl3 concentration of 0.5 mol L-1 was also tested in this work; however, it caused excessive etching of the aluminum substrate.
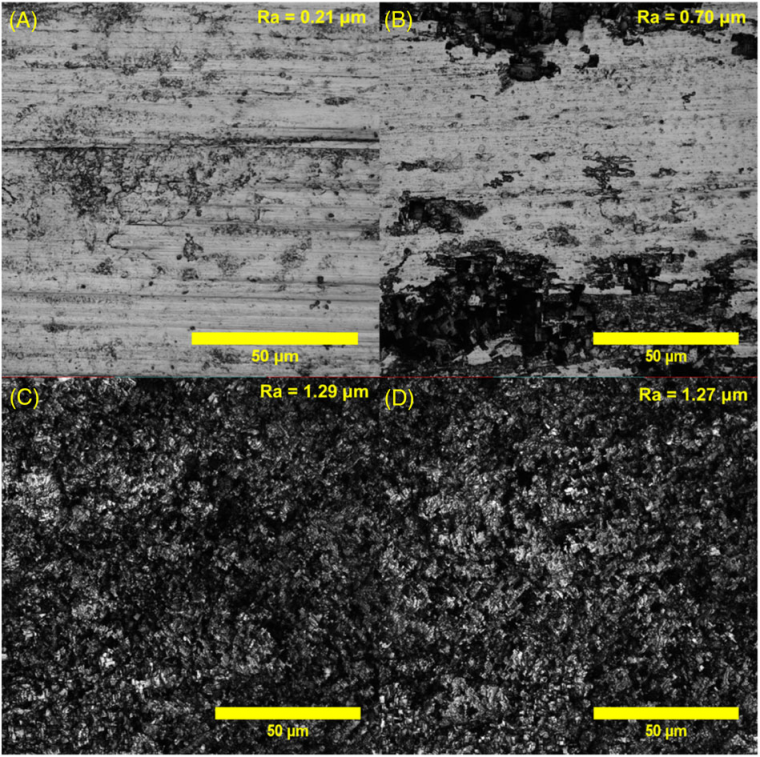
Figure 3 shows the WCA as a function of FeCl3 concentration in the FHH solution, followed by ORMOSIL coating from the PFOTES precursor. Non-etched (NE) and chemically etched samples with a FeCl3 concentration of 0.05 mol L-1 showed similar average WCA values around 120°. The etched samples with a concentration of 0.1 mol L-1 and 0.25 mol L-1 showed relatively high WCAs, but not enough to reach for super-hydrophobicity (WCA > 150°). These results demonstrate that roughness really acts as a wettability amplifier, turning the hydrophobic character of the PFOTES ORMOSIL coating more hydrophobic.
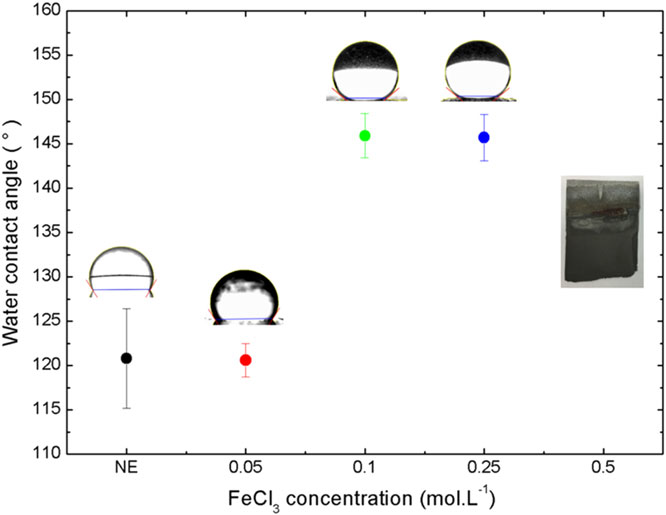
The confocal microscopy images of the aluminum surfaces etched with a FeCl3 concentration of 0.1 mol L-1 with immersion times of 5, 7, 10, and 15 minutes, and the corresponding Ra values are presented in Figure 4. The images show that the morphologies are similar. However, the roughness slightly increases, followed by a gradual decrease as a function of the immersion time. For times greater than 7 minutes, the rough micro-structure was slowly destroyed, decreasing the roughness until complete embrittlement.
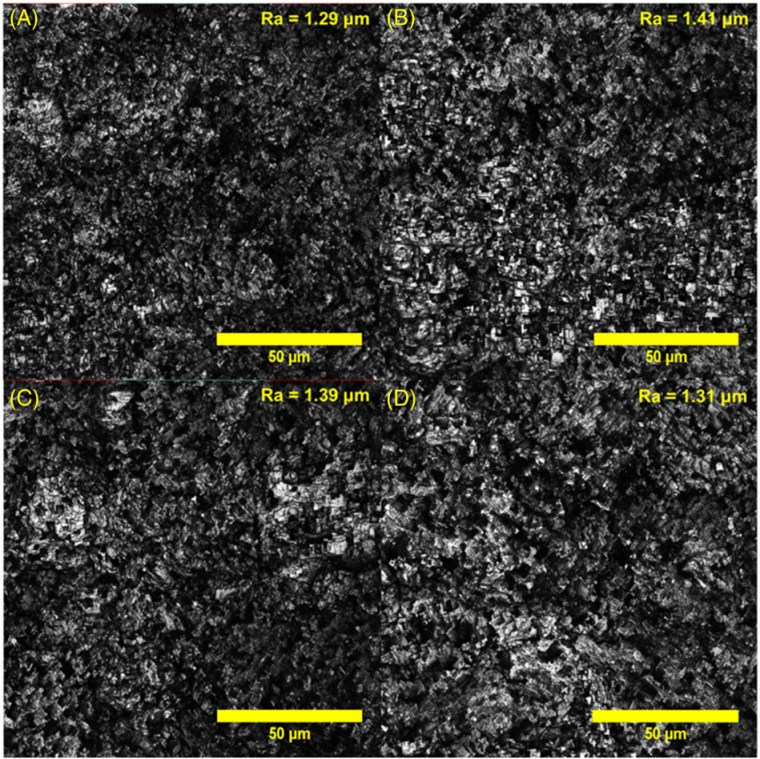
In Figure 5 are presented the WCA as a function of the etching time after PFOTES ORMOSIL deposition. It can be observed that all chemical etching with an immersion time of at least 5 minutes increased the hydrophobicity of the coated surface. However, only the time of 7 minutes provided the roughness necessary to obtain super-hydrophobicity, (WCA = 154.1°).
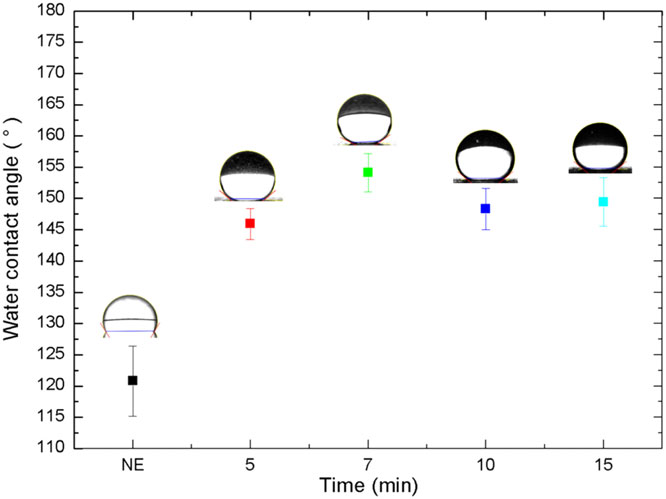
Figure 6 shows the WCA obtained for the uncoated samples and coated ones with the different ORMOSIL coatings and not-etched (NE) aluminum substrates. WCA measurements were also made on substrates coated with ORMOSIL based on TEOS precursor, which do not have hydrophobic groups, for comparison.
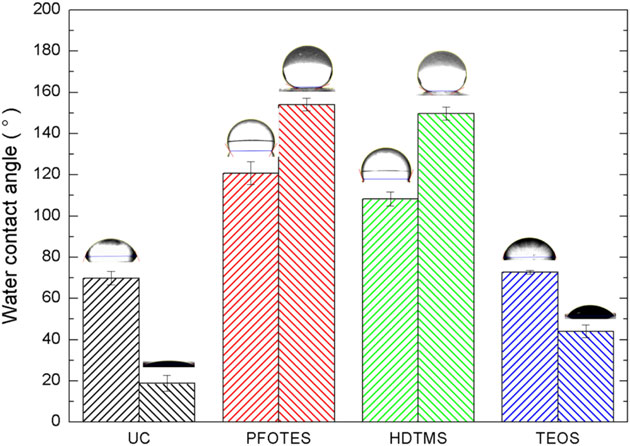
As-received and chemically etched substrates without ORMOSIL coating are hydrophilic (WCA < 90°). Non-etched aluminum substrates coated with ORMOSIL coating based on PFOTES and HDTMS became hydrophobic, with their contact angle increased to 120° and 110°, respectively. For etched and coated samples, the WCAs reached values above 150°. Such evidence demonstrates that the rough surface enhanced the surface’s intrinsic property, hydrophilic surfaces become more hydrophilic, and the hydrophobic surface becomes more hydrophobic, which is in agreement with the Wenzel model. [30] The high surface area of the rough surface (Wenzel model) or air trapped between the droplets and the rough hierarchical structure of the coated surface (Cassie-Baxter model) increased the hydrophobic property of the coating to reach a super-hydrophobic behavior. [30] Moreover, this behavior is also observed for the TEOS-coated samples, where the hydrophobicity increased for etched surfaces.
Figure 7 shows the mineral OCA measured with NE and etched aluminum substrates, uncoated (UC), and coated with ORMOSIL based on PFOTES and HDTMS. Compared with water wettability results, the values obtained are lower, suggesting a higher affinity of the surfaces with oil. This characteristic is justified considering the lower surface tension of mineral oil (30 mJ m-2) than the water one (72 mJ m-2). [57] The coated sample with PFOTES without etching exhibited oleophilic behavior (OCA <90°), which can be attributed to the van der Waals forces between the apolar alkyl chains and the mineral oil. The OCA of the same film deposited on an etched surface greatly increased to 137°. This result is in opposition to the Wenzel model that can only amplify the surface’s intrinsic behavior, as mentioned previously. However, this behavior can be explained by the Cassie-Baxter model, where the air is entrapped in the material roughness, and the oil drop is deposited on a composite surface with oleophobic behavior. [30] The HDTMScoated surfaces appeared to be oleophilic, both etched and NE substrates. The long apolar alkyl chains with only carbon and hydrogen atoms of HDTMS are responsible for the good spreading of oil. Moreover, the etching treatment of the aluminum surface-enhanced classically oleophilic property following the Wenzel model. In this case, we can infer that the surface is not oleophilic enough to let air pockets in the rough structure to repeal the oil spreading. On the contrary, due to a smaller dispersive component of its surface energy and high roughness, the PFOTES-coated sample succeeds to be super-hydrophobic and oleophobic. In this sense, the influence of the roughness shows again to be fundamental.
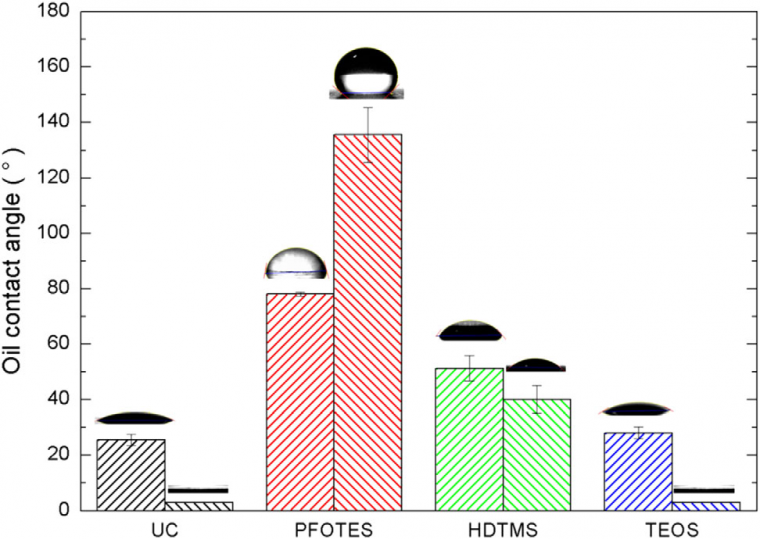
The TEOS ORMOSIL coating shows that the OCA values obtained on NE samples were about 30°. The smaller OCA measured for this sample, compared with the HDTMS and PFOTES coated ones, corroborate results discussed in previous work showing that the dispersive component of the surface energy, responsible for the oil spreading, is higher for the surface with few alkyl chains than for the one with more of such groups. [31] Finally, as expected for such oleophilicity, the etching process increased the oil spreading on TEOS-coated surface, in agreement to the Wenzel model.
Conclusions
To conclude, super-hydrophobic and oleophobic coatings were fabricated on the surface of 1200 H14 aluminum alloy. The aluminum surface roughness was optimized via an etching treatment using an FHH solution. A FeCl3 concentration of 0.1 mol L-1 and an immersion time of 7 min were determined to be optimal to enhance the surface roughness and the hydrophobicity after the deposition of ORMOSIL coatings using HDTMS and PFOTES sol-gel precursors. The etching treatment leads to a homogeneously rough surface with square pores with edges about 1 μm–2 μm. WCA measurements indicated that all etched surfaces functionalized with ORMOSIL showed super-hydrophobic properties. Finally, OCA showed that etched surfaces coated with s so-gel solution using PFOTES were oleophobic due to air entrapment at the oil-surface interface.
References
[1] Y. Liu, Y. Bai, J. Jin, L. Tian, Z. Han, L. Ren, Appl. Surf. Sci. 2015, 355, 1238.
[2] D.D., La, T.A. Nguyen, S. Lee, J.W. Kim, Y.S. Kim, Appl. Surf. Sci. 2011, 257 (13), 5705.
[3] L. Li, V. Breedveld, D.W. Hess, ACS Appl. Mater. Interfaces. 2012, 4 (9), 4549.
[4] T. Darmanin, F. Guittard, Mater. Today 2015, 15, 273.
[5] J.T. Simpson, S.R. Hunter, T. Aytug, Rep. Prog. Phys. 2015, 78 (8), 86501.
[6] A. Milionis, E. Loth, I.S. Adv. Colloid Interface Sci. 2016, 229, 57.
[7] Z. Wang, M. Elimelech, S. Lin, Environ. Sci. Technol. 2016, 50, 5, 2132.
[8] Q. Wen, Z. Guo Chem. Lett. 2016, 45 (10), 1134.
[9] E.V. Bryuzgin, V.V. Klimov, S.A. Repin, A.V. Navrotskiy, I.A. Novakov, Appl. Surf. Sci. 2017, 419, 454.
[10] C. Chen, S. Yang, L. Liu, et al., J. Alloys Compd. 2017, 711, 506.
[11] Z. Xu, Z. Liu, P. Song, C. Xiao Desalination. 2017, 414, 10.
[12] X. Zhao, B. Yu, J. Zhang, J. Colloid Interface Sci. 2017, 501, 222.
[13] H. Zhu, Z. Guo, W. Liu, Chem. Commun. 2014, 50 (30), 3900.
[14] R. Wu, G. Chao, H. Jiang, Y. Hu, A. Panm Mater. Lett. 2015, 42, 176.
[15] A. Vilcnik, I. Jerman, A.S. Vuk, et al., Langmuir 2009, 25 (10), 5869.
[16] Z.S. Saifaldeen, R. Khedir, K.R. Khedir, M.F. Cansizoglu, T. Demirkan, T. Karabacak, J. Mater. Sci. 2014, 49 (4), 1839.
[17] M. Nosonovsky, B. Bhushan, Curr. Opin. Colloid Interface Sci. 2009, 14 (4), 270.
[18] Z. Chu, S. Seeger, Chem. Soc. Rev. 2014, 43 (8), 2784.
[19] T. Jiang, Z. Guo, Chem. Lett. 2015, 44 (3), 324.
[20] M. Guo, B. Ding, X. Li, X. Wang, J. Yu, M.J. Wang, Phys. Chem. C 2010, 114 (2), 916.
[21] M. Ma, R.M. Hill, Curr. Opin. Colloid Interface Sci. 2006, 11 (4), 193.
[22] P. Zhang, F.Y. Lv, Energy 2015, 82, 1068.
[23] D. Lai, D. Kong, C. Che, Surf. Coat. Technol. 2017, 315, 509.
[24] R.G. Wankhede, M. Shantaram, K. Thanawala, A. Khanna, N. Birbillis, J. Mater. Sci. Eng. A 2013, 3, 224.
[25] D. Zhang, L. Wang, H. Qian, X. Li, J. Coat. Technol. Res. 2016, 13 (1), 11.
[26] O. Çakir, J. Mater. Process Technol. 2008, 199, 337.
[27] P.N. Rao, D. Kunzru, J. Micromech. Microeng. 2007, 17 (12), N99.
[28] X. Pan, J. Wu, Y. Ge, et al., J. Sol-Gel Sci. Technol. 2014, 72 (1), 8.
[29] J.D. Mackenzie, E.P. Besche, J. Sol-Gel Sci. Technol. 1998 13, 371.
[30] M. Houmard, E.H.M. Nunes, D.C.L. Vasconcelos, et al., Appl. Surf. Sci. 2014, 289, 218.
[31] M. Houmard, D.C.L. Vasconcelos, W.L. Vasconcelos, G. Berthomé, J.C. Joud, M. Langlet, Surf. Sci. 2009, 603 (17), 2698.
Original publication:
Source: Preview Image: pawel.gaul/Getty Images