Wettability of Low Weight Borides by Commercial Aluminum Alloys − A Basis for Metal Matrix Composite Fabrication
Boron compounds are promising candidates for reinforcing metals because of their high strength and stiffness at low specific weights. For composite fabrication, wetting behavior is important. Isothermal wetting of B4C, AlB2, CaB6, MgB2, and TiB2 by liquid pure aluminum (99.5%) and the alloy AlSi10MgMn was studied at 700 °C for 15 min in vacuum using the dispensed drop method. No wetting occurred for all substrates during testing. The contact angles remained constant for CaB6, MgB2, and TiB2, while those for AlB2 and B4C decreased continuously with time.
Introduction
Particulate reinforced aluminum metal matrix composites (MMCs) combine the beneficial properties of aluminum (low density and high ductility) and ceramic reinforcement materials (high strength and modulus), making them attractive engineering materials for the aerospace and automotive industry [1,2]. The most commonly used manufacturing processes for particulate reinforced MMCs are powder metallurgical and casting processes [2,3]. Aluminum casting is typically performed at approximately 700 °C; thus, the particulate reinforcements should be stable under these conditions. To obtain stiff and lightweight MMC parts, the reinforcement particles should increase the mechanical properties and decrease the density of the composite. Depending on the loading geometry, the effect of density may be more important than the mechanical properties, which is why low weight metal borides are attractive reinforcement materials.
Various metal borides are available; some of them are summarized in Table 1. In this study, we focused on stiffness, whereby particles with high Young's modulus and low density provide the greatest enhancement in composite stiffness. TiB2 promises the most efficient enhancement in Young's modulus; however, taking the density into account, the highest specific stiffness can be achieved by adding CaB6 and B4C (Figure 1).

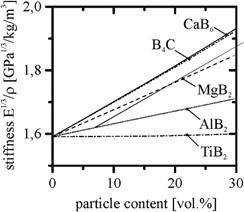
Many attempts have been made to disperse ceramic particles in liquid aluminum alloys, but the poor wettability of most ceramic particles with liquid aluminum promotes the agglomeration of particles in the melt and hinders homogenous particle distribution.
There are different testing procedures to measure the contact angle and thus the wetting behavior of aluminum in contact with ceramic substrates. In the classical sessile drop procedure, the ceramic substrate and aluminum sample are jointly heated from room temperature (contact heating), whereas in the dispensed drop procedure, the aluminum sample is heated separately and squeezed onto the substrate from above (non‐contact heating). In the dispensed drop procedure, the liquid aluminum drop is free of oxides; that is, the result is supposed to be free from artifacts, at least at the beginning of the test [4].
While there are studies on the wetting properties of TiB2 and B4C with pure aluminum, no data on the wetting properties of AlB2, CaB6, and MgB2 with liquid aluminum and its alloys have been published so far.
Therefore, in this study, the wetting behavior of the aluminum alloys Al99.5 and AlSi10MgMn with the substrates AlB2, B4C, CaB6, MgB2, and TiB2 was investigated at a moderate temperature (700 °C) and time (15 min) using the dispensed drop method.
Methods
The boride substrates for the wetting investigations were produced via hot pressing, and their densities were measured using a helium pycnometer and compared with the theoretical and bulk densities to quantify the amount of porosity. After grinding and polishing, the surface roughness of the substrates was measured using an Olympus LEXT OLS 4000 laser scanning microscope. The properties of the ceramic substrates are listed in Table 1.
The wetting kinetic tests were performed at the Foundry Research Institute (Cracow, Poland). A detailed description of the experimental procedure can be found in Eustathopoulos et al. [4] and Sobczak et al. [5]. The dispensed drop method was applied in all tests to produce oxide‐free droplets [4]. For this purpose, the aluminum sample was placed in an alumina capillary located above the substrate inside a molybdenum furnace and then (non‐contact) heated to 700 °C within 60 min in vacuum (<10−5 mbar). When the testing temperature was reached, the melt was pushed and dropped onto the substrate. Images of drop/substrate couples at 700 °C were recorded for 15 min using a high‐resolution CCD camera, and contact angles were calculated.
Results and Discussion
Depending on the initial powder size and hot pressing parameters of the ceramic substrates, the density and corresponding porosity varied over a wide range (Table 1). For AlB2, the bulk and pycnometer densities differed significantly from the theoretical density. This could be due to an incomplete reaction between the aluminum and boron powder during hot pressing, resulting in a mixture of boron, aluminum, and AlB2 phases. The amount of total porosity (i.e., the difference between the theoretical and bulk density) can be divided into the closed and open porosity; the latter influences the surface roughness and wetting properties of the material. Although all substrates were polished in the same way, their surface roughness varied from 0.3 to 2.98 μm due to differences in their open porosity. Rough surfaces can affect the spreading of the liquid drop, leading to apparent contact angles [4,6]. Although MgB2 exhibited a large amount of open porosity, its roughness was lower than that of TiB2, AlB2, and CaB6 because of differences in the hot pressing process and initial powder size. Moreover, polishing can clog the pores of the surface, and as a result, lower surface roughness is measured by laser scanning microscopy while still a large amount of open porosity can occur as the helium pycnometer measurement is not affected by surface clogging.
Figure 2 illustrates the time-dependent wetting behavior of the investigated ceramic substrates with Al99.5 and the AlSi10MgMn alloy at 700 °C for 15 min. No wetting (contact angle θ > 90°) occurred for all examined couples. The contact angles for Al99.5 were higher than those for AlSi10MgMn, except for the MgB2 substrate in which case the contact angle for Al99.5 was slightly lower (~4°). The reason for the lower contact angles for the AlSi10MgMn alloy is that most alloying elements, especially the combined addition of silicon and magnesium, reduce the surface tension [7].
Furthermore, different drop spreading characteristics were identified. A non‐wetting behavior with no spreading was observed for CaB6, MgB2, and TiB2. The contact angles remained almost constant for 15 min for both the pure aluminum and alloy. Consequently, the height and diameter of the liquid drop also remained constant (Figure 2). The initial contact angles measured immediately after drop dispensing were approximately 126°–127° for AlSi10MgMn on CaB6, MgB2, and TiB2 and 134°–136° for Al99.5 on CaB6 and TiB2. After 15 min, the contact angle for Al99.5 on TiB2 decreased by 3°–4°, and the drop diameter increased slightly by 5%. However, these changes were too small to assume a reactive wetting behavior. Even the large amount of open porosity did not lead to the infiltration of liquid aluminum.
A different wetting behavior was observed for AlB2 and B4C for which drop spreading occurred with time. Liquid aluminum reportedly reacts with B4C by forming intermetallic phases; however, the wettability is poor at temperatures below 900 °C [8,9]. The initial contact angles were 118° and 126° for AlSi10MgMn and Al99.5 on B4C, respectively. A decrease in the contact angle by 11°–13° and slow spreading were observed along the B4C surface as the drop diameter increased, and the drop height decreased during testing.
Both Al99.5 and AlSi10MgMn penetrated the AlB2 substrate during testing, leading to decreased drop heights but constant drop diameters. The initial contact angles after drop deposition were 119° and 129° for AlSi10MgMn and Al99.5, respectively, which after 15 min decreased to 107° and 120°, respectively. The AlB2 substrate was probably a mixture of boron, aluminum, and AlB2 phases, significantly influencing its wetting behavior. In the absence of disturbing oxide layers, liquid metals wet metal surfaces. Therefore, aluminum impurities present in the substrate could exhibit strong adhesive interactions with the liquid aluminum drop, forcing the spreading of the drop. However, due to the open porosity and surface roughness of the substrate, the liquid aluminum drop preferred to infiltrate the AlB2 substrate.
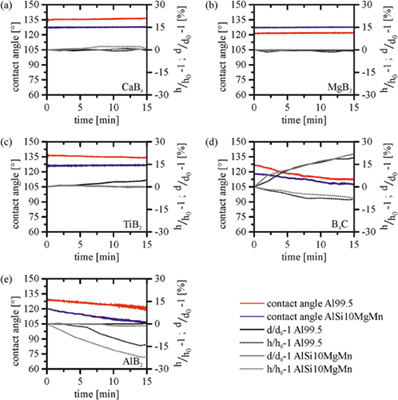
Conclusion
The wetting behavior of the liquid aluminum alloys Al99.5 and AlSi10MgMn on B4C, AlB2, CaB6, MgB2, and TiB2 was investigated at 700 °C for 15 min via the dispensed drop technique. No wetting occurred within 15 min for all substrates and alloys. The contact angles of both aluminum alloys remained almost constant on CaB6, MgB2, and TiB2 during testing. However, for B4C and AlB2, changes in the drop shape were observed, indicating reactive wetting. In addition, alloying elements reduced the contact angles of AlSi10MgMn, which were lower than those of Al99.5 on most substrates.
References
[1] M. K. Surappa, J. Mater. Process. Technol. 1997, 63, 325.
[2] K. U. Kainer, in Metal Matrix Composites Custom‐Made Materials for Automotive and Aerospace Engineering, Wiley‐VCH, Weinheim 2006.
[3] I. A. Ibrahim, F. A. Mohamed, E. J. Lavernia, J. Mater. Sci. 1991, 26, 1137.
[4] N. Eustathopoulos, N. Sobczak, A. Passerone, K. Nogi, J. Mater. Sci. 2005, 40, 2271.
[5] N. Sobczak, R. Nowak, W. Radziwill, J. Budzioch, A. Glenz, Mater. Sci. Eng. A 2008, 495, 43.
[6] S. J. Hitchcock, N. T. Carroll, M. G. Nicholas, J. Mater. Sci. 1981, 16, 714.
[7] I. F. Bainbridge, J. A. Taylor, Metall. Mater. Trans. A 2013, 44A, 3901.
[8] Q. L. Lin, P. Sheng, F. Qiu, D. Zhang, Q. C. Jiang, Scr. Mater. 2009, 60, 960.
[9] D. C. Halverson, A. J. Pyzik, I. A. Aksay, W. E. Snowden, J. Am. Ceram. Soc. 1989, 72, 775.
Original publication:
Ploetz, S., Nowak, R., Lohmueller, A., Sobczak, N. and Singer, R.F. (2016), Wettability of Low Weight Borides by Commercial Aluminum Alloys − A Basis for Metal Matrix Composite Fabrication . Adv. Eng. Mater., 18: 1884-1888. https://doi.org/10.1002/adem.201600297
Source: Preview Image: Zffoto/Getty Images