Micro‐Structuration of Piezoelectric Composites Using Dielectrophoresis: Toward Application in Condition Monitoring of Bearings
A piezoelectric material based on inorganic/organic composites suitable for aerospace and aeronautical monitoring sensors was fabricated. The designed piezoelectric composite was made of a lead zirconate titanate (PZT) filler embedded in a polydimethylsiloxane (PDMS) matrix. To improve the piezoelectric properties of the film, we increased the connectivity of the ceramic filler via electric field‐assisted structuration, leading to a columnar arrangement of the filler across the thickness. This structure (1–3) showed higher piezoelectricity than one with a randomly dispersed filler (0–3). Piezoelectric and dielectric activities of PZT/PDMS in 0–3 and 1–3 configurations were compared at different volume fractions. The 1–3 connectivity led to superior piezoelectric behavior. Thermal stability and high-temperature X‐ray diffraction analyses indicated that the composites were stable and maintained a good piezoelectric response even at 200 °C. Following process optimization, the piezoelectric behavior of this new class of composites approached that of fluorinated ferroelectric polymers, with the advantage that the stability of the piezoelectric properties was preserved at a higher temperature and lower poling electric field. In conclusion, there is potential for integrating the designed sensor in aircraft ball bearings for condition monitoring.
Introduction
In aeronautics and aerospace, there is a growing need for new sensor materials suitable for direct health condition monitoring of complex structures. The main requirements when designing such sensors are sensibility, frequency bandwidth, and temperature drift [1,2]. For simple system integration, these sensors must also be light and non‐intrusive for the system with high mechanical resistance and easy processability.
Due to their ability to translate a mechanical impulse into an electric response, piezoelectric materials are commonly used as sensors in vibration monitoring, impact detection, and ultrasonic receiving sensors [2–5]. Different classes of piezoelectric materials exist, such as ferroelectric ceramics, piezoelectric polymers, and piezoelectric composites made of a ferroelectric ceramic filler embedded in a polymer matrix. Piezoelectric composites are most suitable for the above applications as they combine the piezoelectric properties of the filler with the flexibility of the matrix [5]. Furthermore, they are characterized by a low poling electric field and high Curie temperature, making them more suitable than ferroelectric polymers [6]. Being well workable, piezoelectric composites can be simply integrated into complex designs [5].
Phase arrangement is a key factor influencing the piezoelectric properties of a composite. Composites with 0–3 connectivity are most commonly produced because of their simple fabrication. However, they exhibit low piezoelectric sensibility until they reach large volumetric filler contents, which in turn deteriorate the mechanical properties [7]. A solution to this problem is to align the fillers in columns within the matrix. In such anisotropic structures, called 1–3, the particles are closely aligned along the preferred direction, enhancing the piezoelectric properties of the whole material [4,5].
Introduction
In aeronautics and aerospace, there is a growing need for new sensor materials suitable for direct health condition monitoring of complex structures. The main requirements when designing such sensors are sensibility, frequency bandwidth, and temperature drift [1,2]. For simple system integration, these sensors must also be light and non‐intrusive for the system with high mechanical resistance and easy processability.
Due to their ability to translate a mechanical impulse into an electric response, piezoelectric materials are commonly used as sensors in vibration monitoring, impact detection, and ultrasonic receiving sensors [2–5]. Different classes of piezoelectric materials exist, such as ferroelectric ceramics, piezoelectric polymers, and piezoelectric composites made of a ferroelectric ceramic filler embedded in a polymer matrix. Piezoelectric composites are most suitable for the above applications as they combine the piezoelectric properties of the filler with the flexibility of the matrix [5]. Furthermore, they are characterized by a low poling electric field and high Curie temperature, making them more suitable than ferroelectric polymers [6]. Being well workable, piezoelectric composites can be simply integrated into complex designs [5].
Phase arrangement is a key factor influencing the piezoelectric properties of a composite. Composites with 0–3 connectivity are most commonly produced because of their simple fabrication. However, they exhibit low piezoelectric sensibility until they reach large volumetric filler contents, which in turn deteriorate the mechanical properties [7]. A solution to this problem is to align the fillers in columns within the matrix. In such anisotropic structures, called 1–3, the particles are closely aligned along the preferred direction, enhancing the piezoelectric properties of the whole material [4,5].
In this study, dielectrophoresis was used to develop a piezoelectric sensor coating consisting of a polydimethylsiloxane (PDMS) matrix filled with lead zirconate titanate (PZT) particles. The effect of the particles' alignment on the piezoelectric and dielectric properties was investigated using 0–3 and 1–3 PZT/PDMS composites with particle volume contents ranging from 3.2% to 24%. The thermal stability and influence of the poling electric field amplitude on the piezoelectric properties of the composites were also investigated. Furthermore, the dielectrophoresis process was examined for its dependence on the electric field frequency. Finally, as piezoelectric composites are widely exploited in the health monitoring system of structural components [4,5], a potential application is described, indicating that the proposed 1–3 material sensor is suitable for condition monitoring in aircraft bearings.
Methods
For sample fabrication, linear vinyl terminated PDMS consisting of a base and a cross-linker was selected as the matrix and PZT as the piezoelectric phase. PZT powder and silicone base were mixed by ultrasonication, and the cross‐linker was added at a ratio of 1:10 (curing agent/base). The 0–3 composites were prepared by casting the dried mixture as a film on a glass substrate. The casting film was cured for 30 min at 120 °C. Finally, the fabricated films were cut into circular shapes, and gold electrodes were sputtered onto both sides of the composites. The 1–3 composites were prepared by pouring the dried mixture into a mold positioned between two aluminum plates. The aluminum plates acted as electrodes for the structuring field. The mold was first incubated for 15 min at 25 °C and then for 1 h at 120 °C. During incubation, an AC electric field (amplitude, 2 V μm−1) was applied, leading to aligned particle chains along the poling direction. Samples in both 0–3 and 1–3 configurations were prepared with different PTZ volume contents (3.2%, 12%, and 24%).
The dielectric permittivity of the 0–3 and 1–3 PZT/PDMS composites was determined by dynamic dielectric spectroscopy. To assess the piezoelectric behavior of the composites as a function of particle volume fraction (φ), all samples were poled at 100 °C for 30 min under an applied DC electric field (amplitude, 20 V μm−1). Composites with the same filler content (24%vol) were poled under different electric fields (5, 10, 20, and 30 V μm−1) to evaluate the dependence of the piezoelectric behavior on the poling electric field. In addition, the piezoelectric charge coefficient (d33) of all samples was determined and evaluated as a function of the volume fraction and the poling electric field.
To investigate the thermal stability of the piezoelectric composites, we used samples with the same particle content (24%vol). After poling, the composites were annealed for 10 min in a short circuit at various temperatures (25 °C, 50 °C, 100 °C, 150 °C, and 200 °C). The samples were then cooled to 25 °C, and the d33 response was recorded. The morphology and structure of the composites were investigated by X-ray diffraction (XRD) at 25 °C, 150 °C, and 200 °C.
For the dielectrophoresis process, two parallel strips of conductive tape (electrodes) spaced 1 mm apart were placed on a glass microscope slide. A 3.2%vol PZT/PDMS solution was placed on the slide. After applying an electric field between the two stripes, the dependence of the particle's alignment on the electric field frequency was studied at 2 Hz and 2 kHz (constant amplitude, 2 V μm−1). The microstructures of the particle chains were observed with an Olympus BH microscope.
The full article of this digest includes a detailed description of 0–3 and 1–3 connectivity models.
Results and Discussion
The dielectric permittivity of the structured sample (1–3) was significantly greater than that of the randomly dispersed sample (0–3). Compared with the 0–3 composites, the 1–3 composites filled with 12%vol and 24%vol PZT showed an approximate three- and twofold increase in permittivity, respectively. In 1–3 composites, the dielectric particles are closely packed in the alignment direction and less shielded by the polymer matrix, causing a higher permittivity in the column direction. This is the first proof that dielectrophoresis induces a significant change in the dielectric properties of composites. The dielectric permittivity of the 1–3 composites was comparable to that of fluorinated ferroelectric polymers [8].
The 1–3 composites also exhibited markedly enhanced d33 values, regardless of their volume content. This can be explained by the more favorable distribution of the electric field in structured composites, allowing greater polarization. Plotting the d33 values of the 1–3 composite (24%vol PZT) against increasing poling field amplitudes revealed a saturation of the poling level at 20 V μm−1 above which all the dipoles in the particles were oriented. Higher electric fields did not further increase the piezoelectric response. Even at this low poling field, the d33 value of the 1–3 composite was similar to that of classical ferroelectric polymers, which usually require an electric field of >100 V μm−1.
The piezoelectric activity of the composites was also analyzed at high temperatures to investigate their thermal stability. Both 0–3 and 1–3 PZT/PDMS (24%vol PZT) composites maintained their piezoelectric activity up to a temperature of 100 °C, above which d33 started to decrease gradually. Between 150 °C and 200 °C, d33 decreased by 20%–30% due to some temperature-induced structural changes in the crystalline cells. Beyond 350 °C, which is the Curie temperature of PZT, the PZT particles exhibit a morphotropic phase boundary (MPB) perovskite structure, whereas, above the Curie temperature, the cell structure is cubic [9]. The MPB cell is formed by the coexistence of rhombohedral and tetragonal ferroelectric phases, whereas the cubic cell is symmetrical and paraelectric [9]. In the high-temperature XRD analysis, the rhombohedral phase peak of the 0–3 and 1–3 samples decreased with increasing temperature, leading to an increase in the tetragonal phase. At 200 °C, the symmetry was only tetragonal. This was more noticeable in 0–3 than in 1–3 composites, indicating that the lattice stability of the structured composites was higher. These results indicate that the present composites, regardless of their structure (random or aligned), can withstand temperatures up to 200 °C without significantly changing their piezoelectric behavior. This makes them more suitable for high‐temperature applications than classical ferroelectric polymers, which are more temperature-sensitive.
Electrically induced structures in 0–3 and 1–3 PZT/PDMS composites with volume fractions of 3.2%vol and 12%vol were visually observed. In the 0–3 sample (3.2%vol), the particles dispersed randomly (Figure 1a), whereas, in the 1–3 sample (3.2%vol), they exhibited a chain‐like structure (Figure 1b). In the 1–3 PZT/PDMS composite with 12%vol PZT, the filler arranged in a columnar disposition with denser columns due to the increased volume fraction (Figure 1c).
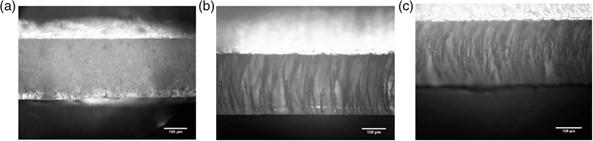
The dependence of the dielectrophoresis process on electric field frequency was analyzed. Figure 2 shows the isotropic structure of the 0–3 composite before the process and the aligned inorganic particles within the polymer matrix after applying an electric field at different frequencies (2 Hz and 2 kHz). Structuring was more effective at 2 Hz as the particle columns were more defined and continuous than those obtained at 2 kHz. The average thickness of the columns was 23.9 μm at 2 kHz and 48.6 μm at 2 Hz. Moreover, the d33 value of the 1–3 composite (24%vol) processed at 2 Hz was 28% higher than that of the composite processed at 2 kHz.
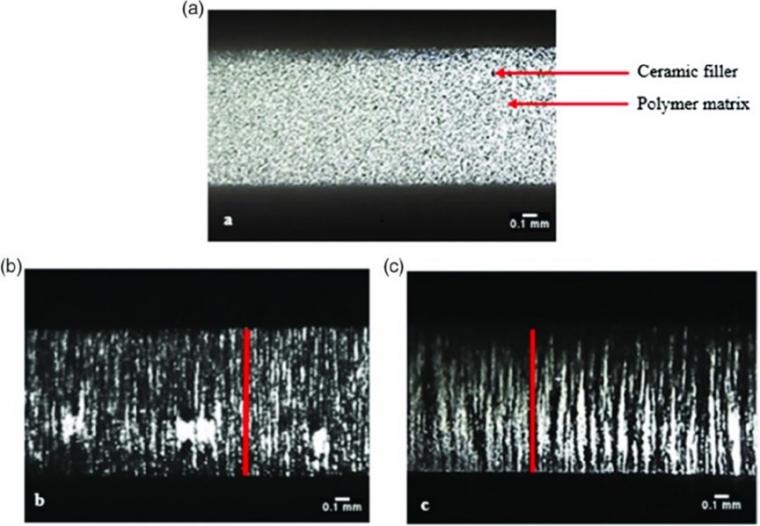
The present composites were then compared with other piezoelectric composites and polymers in terms of d33, poling electric field (EPol), and volumetric fraction of the crystalline phase (φCr). On the basis of these parameters, a figure of merit [FoM = d33/(EPo × φCr)] was calculated, indicating the profitability of the materials (Table 1). According to this FoM, the 1–3 PZT/PDMS composite is superior to other reported materials [10–17].
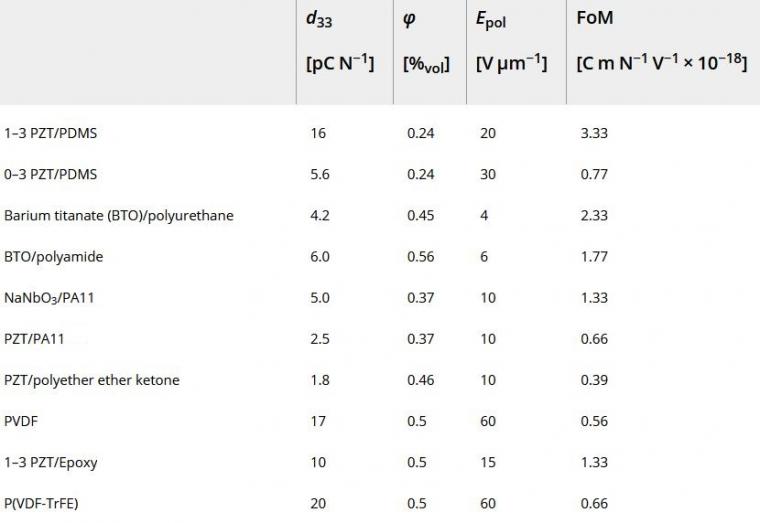
Rolling‐element bearings are an important part of jet engines, and condition monitoring can help detect bearing faults and predict bearing life. However, the development of smart bearing coatings is complex because of the extreme bearing environment (e.g., high shaft rotational speed, vibration, and temperature). Piezoelectric coatings are promising candidates for developing smart bearings as they are thermally stable and easy to process. Figure 3 shows the implementation of the present piezoelectric layer on a bearing.
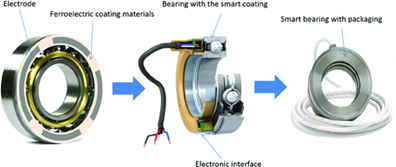
The sensing response of the piezoelectric coating was compared with that of a classical accelerometer. Regarding the temporal response, the signals of both sensors had a similar appearance of vibrations; that is, the amplitude was relatively small and steady before rotation but varied and increased significantly during rotation (Figure 4a). This observation indicates that piezoelectric materials can provide information on the vibration. To further analyze these responses, we performed a fast Fourier transform (FFT)-based frequency method. Figure 4b shows the frequency content of the sensing signal of the piezoelectric coating and the classical accelerometer, which is a simple way to locate frequencies characteristic of faults [18]. The frequency spectra of both sensors differed as they represented different physical quantities. The piezoelectric coating reflected bearing deformations, the frequency harmonics of which (multiples of 12 Hz) were lower than those produced by the accelerometer (50 Hz), which in contrast were related to bearing rotation. Based on the frequency-time analysis shown in Figure 4b, variations in rotational speed could be identified.
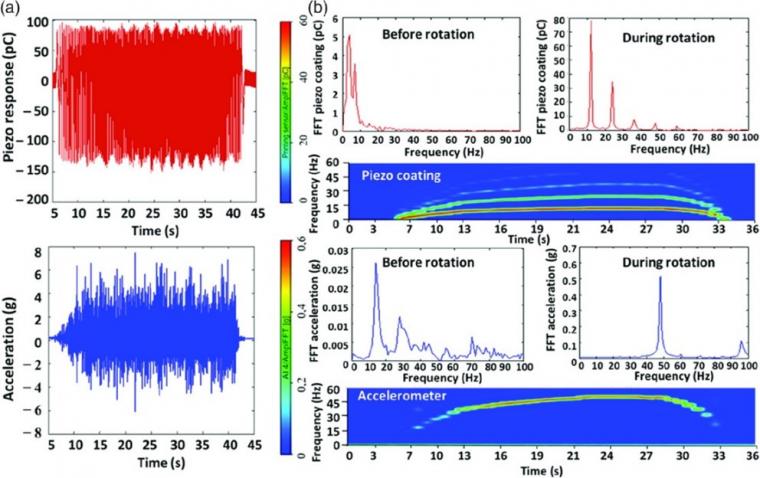
Conclusion
This work highlights the effects of dielectrophoresis on piezoelectric composites made of a silicone matrix doped with PZT particles. The columnar arrangement of particles along the field direction led to significantly improved dielectric and piezoelectric performances. The d33 values of 1–3 composites were markedly higher than those of 0–3 composites, regardless of their PZT concentration. The achieved properties make 1–3 composites an excellent alternative to classical ferroelectric polymers as they exhibit similar piezoelectric properties but at a lower poling electric field. The piezoelectric activities of the 0–3 and 1–3 composites were thermally stable up to 200 °C. XRD analysis confirmed the structural stability of the composites at different temperatures. These results indicate that the present composites are more suitable for high‐temperature environments than ferroelectric polymers. Furthermore, the 1–3 composite was superior to other piezoelectric composites and organic ferroelectric polymers in terms of piezoelectric activity, filler volume content, and poling field. Therefore, the 1–3 piezoelectric material is an excellent candidate for various applications in multifunctional sensing devices, particularly for condition monitoring of ball bearings in the aeronautic area. By depositing the piezoelectric element on a bearing ring, we could detect local vibrations indicative of imminent bearing failure. Thus, the piezoelectric material represents a cheap alternative to common accelerometers.
References
[1] H. Hoshyarmanesh, A. Abbasi, J. Intell. Mater. Syst. Struct. 2018, 29, 1799.
[2] T. Zheng, Y. Zhang, Q. Ke, H. Wu, L. W. Heng, D. Xiao, J. Zhu, S. J. Pennycook, K. Yao, J. Wu, Nano Energy 2020, 70, 104559.
[3] S. M. Peelamedu, C. Ciocanel, N. G. Naganathan, Smart Mater. Struct. 2004, 13, 990.
[4] T. Kim, Z. Cui, W.‐Y. Chang, H. Kim, Y. Zhu, X. Jiang, IEEE Trans. Ind. Electron. 2020, 67, 6955.
[5] H. Kim, T. Kim, D. Morrow, X. Jiang, IEEE Trans. Ultrason. Ferroelectr. Freq. Control 2020, 67, 158.
[6] H. Khanbareh, V. Y. Topolov, C. R. Bowen, Piezo‐Particulate Composites, Springer‐Verlag Berlin Heidelberg 2019, pp. 31– 83.
[7] I. Babu, G. de With, Compos. Sci. Technol. 2014, 91, 91.
[8] J.‐F. Capsal, E. Dantras, J. Dandurand, C. Lacabanne, J. Non. Cryst. Solids 2012, 358, 794.
[9] S. A. Mabud, J. Appl. Crystallogr. 1980, 13, 211.
[10] J.‐F. Capsal, C. David, E. Dantras, C. Lacabanne, Smart Mater. Struct. 2012, 21, 055021.
[11] C. David, J.‐F. Capsal, L. Laffont, E. Dantras, C. Lacabanne, J. Phys. D. Appl. Phys. 2012, 45, 415305.
[12] J.‐F. Capsal, E. Dantras, L. Laffont, J. Dandurand, C. Lacabanne, J. Non. Cryst. Solids 2010, 356, 629.
[13] J.‐F. Capsal, E. Dantras, J. Dandurand, C. Lacabanne, J. Non. Cryst. Solids 2007, 353, 4437.
[14] D. Carponcin, E. Dantras, L. Laffont, J. Dandurand, G. Aridon, F. Levallois, L. Cadiergues, C. Lacabanne, J. Non. Cryst. Solids 2014, 388, 32.
[15] M. Alexandre, C. Bessaguet, C. David, E. Dantras, C. Lacabanne, Phase Transitions 2016, 89, 708.
[16] F. Dominici, D. Puglia, F. Luzi, F. Sarasini, M. Rallini, L. Torre, Polymers 2019, 11, 2097.
[17] N. K. James, D. van den Ende, U. Lafont, S. van der Zwaag, W. A. Groen, J. Mater. Res. 2013, 28, 635.
[18] T. A. Harris, M. N. Kotzalas, Advanced Concepts of Bearing Technology, CRC Press, Boca Raton, FL 2006.
This article is the digest version of the following full paper:
D'Ambrogio, G., Zahhaf, O., Hebrard, Y., Le, M.Q., Cottinet, P.‐J. and Capsal, J.‐F. (2021), Micro‐Structuration of Piezoelectric Composites Using Dielectrophoresis: Toward Application in Condition Monitoring of Bearings. Adv. Eng. Mater., 23: 2000773. https://doi.org/10.1002/adem.202000773
Source: Preview Image: Michal Krakowiak/iStockphoto