Mechanical Properties and Slurry Erosion Resistance of a Hybrid Composite SiC Foam/SiC Particles/EP
The novel hybrid composite SiC foam/SiC particles/EP (SiCfoam/SiCp/EP) was prepared, consisting of an E‐51 epoxy resin (EP) as the matrix and SiCfoam/SiCp particles as the reinforcements. The slurry erosion properties of the SiCfoam/SiCp/EP and SiCfoam/EP (SiC foam/epoxy resin) composites were investigated using a rotating disc rig. SiCfoam/SiCp/EP exhibited better mechanical and anti‐erosive performances than SiCfoam/EP. The SiC particle size had a great impact on the mechanical and anti‐erosive properties of the hybrid composites. Smaller SiC particles improved the mechanical strength but tended to decrease the anti‐erosive performance of the composite. The hybrid composite SiCfoam/SiCp/EP can be applied under solid particle erosion conditions because of its excellent anti-erosive properties.
Introduction
Solid particle erosion, a typical dynamic wear mode, results from the repeated impact of small, solid particles [1]. It occurs in various engineering fields, such as automotive, aerospace, marine, and energetics. Polymers and polymer composites are widely used in engineering fields because of their high specific strength and stiffness [2,3]. The erosive resistance of various polymer composites has extensively been investigated, including fiber‐reinforced or particle‐reinforced composites and hybrid polymer composites. Fiber/matrix adhesion and fiber orientation strongly affect the erosive resistance of fiber-reinforced composites, which show a semi-ductile erosion behavior [4,5]. In particle-reinforced composites, the particle fillers have a significant effect on the erosive performance of the composite [6,7]. The incorporation of particle fillers into fiber-reinforced polymer composites improves the material's erosive resistance. However, the erosive performance of ceramic foam‐reinforced polymer composites is poorly studied even though ceramic foams have attracted much interest in the past decade.
Ceramic foams, with their unique 3D network architecture and outstanding mechanical and anti‐erosive properties, are excellent reinforcements in composite materials [8–11]. The interpenetrating 3D structure of the ceramic foam reinforcement greatly enhances the mechanical and physical performance of composites. For example, the incorporation of SiC foam into SiC particle-reinforced aluminum composites markedly decreased the composite’s thermal expansion because of the interpenetrating structure of the SiC foam [8]. Furthermore, co‐continuous ceramic foam/aluminum composites were up to twice as wear-resistant as metal-matrix composites made of ceramic powder/fibers, indicating that ceramic foams are more efficient than ceramic powder/fibers as reinforcements in aluminum alloys [9]. We previously showed that a SiC foam/epoxy co‐continuous phase composite (SiCfoam/EP) exhibits better slurry erosion resistance than the epoxy matrix alone and the widely used pipeline steel, indicating that SiCfoam/EP composites can be applied under solid particle erosion conditions [11]. The reinforcing effect of SiC foam on the composite's slurry erosion resistance is greater than that of dispersed SiC particles. However, erosion of the epoxy matrix to a certain degree is inevitable, and increasing the volume fraction of SiC foams to enhance the erosive resistance is an inefficient approach because the preparation of SiC foams at high volume fractions is difficult. Therefore, a hybrid composite in which the reinforcing effects of two reinforcements synergize each other is a good choice for improving the erosive resistance.
This article proposes a hybrid SiC foam/SiC particles/epoxy (SiCfoam/SiCp/EP) composite that can be applied under solid particle erosion conditions. SiCfoam/SiCp/EP exhibited not only improved mechanical properties but also desirable slurry erosion resistance. The mechanical properties and slurry erosion resistance of the SiCfoam/EP composite and hybrid composites containing SiC particles of different sizes were systematically compared. The slurry erosion mechanism of the SiCfoam/SiCp/EP composite was also investigated.
Introduction
Solid particle erosion, a typical dynamic wear mode, results from the repeated impact of small, solid particles [1]. It occurs in various engineering fields, such as automotive, aerospace, marine, and energetics. Polymers and polymer composites are widely used in engineering fields because of their high specific strength and stiffness [2,3]. The erosive resistance of various polymer composites has extensively been investigated, including fiber‐reinforced or particle‐reinforced composites and hybrid polymer composites. Fiber/matrix adhesion and fiber orientation strongly affect the erosive resistance of fiber-reinforced composites, which show a semi-ductile erosion behavior [4,5]. In particle-reinforced composites, the particle fillers have a significant effect on the erosive performance of the composite [6,7]. The incorporation of particle fillers into fiber-reinforced polymer composites improves the material's erosive resistance. However, the erosive performance of ceramic foam‐reinforced polymer composites is poorly studied even though ceramic foams have attracted much interest in the past decade.
Ceramic foams, with their unique 3D network architecture and outstanding mechanical and anti‐erosive properties, are excellent reinforcements in composite materials [8–11]. The interpenetrating 3D structure of the ceramic foam reinforcement greatly enhances the mechanical and physical performance of composites. For example, the incorporation of SiC foam into SiC particle-reinforced aluminum composites markedly decreased the composite’s thermal expansion because of the interpenetrating structure of the SiC foam [8]. Furthermore, co‐continuous ceramic foam/aluminum composites were up to twice as wear-resistant as metal-matrix composites made of ceramic powder/fibers, indicating that ceramic foams are more efficient than ceramic powder/fibers as reinforcements in aluminum alloys [9]. We previously showed that a SiC foam/epoxy co‐continuous phase composite (SiCfoam/EP) exhibits better slurry erosion resistance than the epoxy matrix alone and the widely used pipeline steel, indicating that SiCfoam/EP composites can be applied under solid particle erosion conditions [11]. The reinforcing effect of SiC foam on the composite's slurry erosion resistance is greater than that of dispersed SiC particles. However, erosion of the epoxy matrix to a certain degree is inevitable, and increasing the volume fraction of SiC foams to enhance the erosive resistance is an inefficient approach because the preparation of SiC foams at high volume fractions is difficult. Therefore, a hybrid composite in which the reinforcing effects of two reinforcements synergize each other is a good choice for improving the erosive resistance.
This article proposes a hybrid SiC foam/SiC particles/epoxy (SiCfoam/SiCp/EP) composite that can be applied under solid particle erosion conditions. SiCfoam/SiCp/EP exhibited not only improved mechanical properties but also desirable slurry erosion resistance. The mechanical properties and slurry erosion resistance of the SiCfoam/EP composite and hybrid composites containing SiC particles of different sizes were systematically compared. The slurry erosion mechanism of the SiCfoam/SiCp/EP composite was also investigated.
Methods
The SiCfoam/SiCp/EP composite was prepared by a modified procedure previously reported [11]. The SiC foam volume fraction was 60%. The SiC foam had a cell size of ~1.5 mm, and the SiC particles had grain sizes of 0.74, 0.41, and 0.1 mm in SiCp I, SiCp II, and SiCp III, respectively. SiCfoam, consisting of α‐SiC, β‐SiC, and Si, was produced by a solid‐state sintering process. SiC particles were treated with the silane-coupling agent KH‐550 to modify the adhesion between the epoxy matrix and SiC particles. The SiC particles were then dispersed into SiC foam cells to obtain SiCfoam/SiCp. The SiCp volume fraction in the three hybrid composites was ~25%. The epoxy resin was then squeezed into SiCfoam/SiCp by vacuum infiltration and compression molding. The uncured sample was kept in a vulcanization machine at 100 °C and 10 MPa for 4 h to obtain a completely cured epoxy matrix.
For the compression and three‐point bend experiments, the samples were tested at a constant displacement rate of 0.5 mm/min with a load capacity of 100 kN. The impact tests were conducted in a pendulum impact-testing machine with a load capacity of 0.5 J.
Slurry erosion experiments were performed in a rotating disc rig. The slurry consisted of water and erodent quartz sand with a grain size of 70–150 mesh. The sand content was 10 kg/m3, and the flow velocity was kept at 10 m/s. The sample surfaces were ground with a 1000-grit abrasive paper and then cleaned in deionized water and dried before the tests. The slurry erosion of each sample was characterized by the erosion rate (E): E = (m0 - m)/A /t, where m0, m, A, and t represent the initial mass, the mass after the test, the surface area of the sample, and test duration, respectively.
The structures of the SiCfoam/SiCp/EP composites were analyzed using an Olympus SZX16 stereoscopic microscope. The fracture morphologies and microstructures of the composites after the mechanical and slurry erosion tests, respectively, were observed with a scanning electron microscope (SEM) and an Olympus LEXT OLS4000 confocal laser scanning microscope (CLSM).
Results and Discussion
The cured SiCfoam/SiCp/EP hybrid composites showed no voids and piles, and the epoxy matrix/SiC particles and SiC foam interpenetrated mutually. The SiC particles and epoxy matrix were trapped within the SiC foam cells of the interpenetrating composite structures.
The SiCfoam/SiCp/EP composites exhibited better mechanical properties (i.e., compressive strength, flexural strength, and impact toughness) than the SiCfoam/EP composite. Among the SiCfoam/SiCp/EP composites, SiCfoam/SiCp III/EP performed best as the mechanical properties of the hybrid composites increased with decreasing SiC particle size. Therefore, the grain size of the SiC particles plays a pronounced role in the mechanical properties of the SiCfoam/SiCp/EP composites. Reinforcing the epoxy resin by SiC particles improves its mechanical properties and poor resistance to crack growth [12,13]. Therefore, the SiCfoam/SiCp/EP composites exhibited better mechanical properties than the SiCfoam/EP composite. Figure 1 shows the flexural fracture morphologies of the four composites. The failure mechanism of the hybrid composites included the fracture and detachment of SiC particles. Cracks propagated more tortuously in the hybrid composites than in the SiCfoam/EP composite, and the grain size of the SiC particles affected the morphologies markedly. CLSM images of the flexural fractures in SiC foam cells show that the fracture surface of the SiCfoam/EP composite was smoother than that of the SiCfoam/SiCp/EP composites (Figure 2). These observations indicate that more fracture energy is absorbed during SiCfoam/SiCp/EP fracture than during SiCfoam/EP fracture. The roughness of the fracture surface and fracture energy increased gradually with decreasing SiC particle size. Smaller particles have a larger total surface, and the strength of particle‐reinforced composites increases with the particle surface area [14]. Therefore, the mechanical properties of the hybrid composites increased with decreasing grain size.
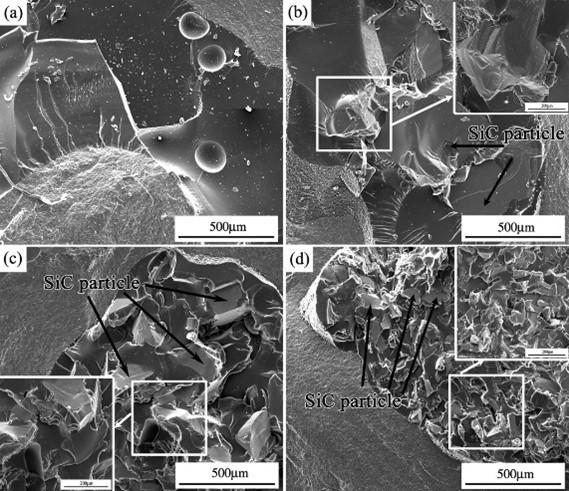
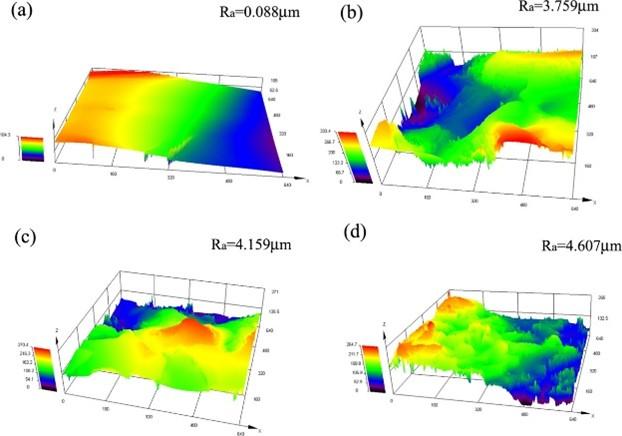
The SiCfoam/SiC/EP composites showed lower erosion rates than the SiCfoam/EP composite. The slurry erosion resistance of SiCfoam/SiCI/EP, SiCfoam/SiCII/EP, and SiCfoam/SiCIII/EP increased by 190%, 94%, and 2%, respectively, compared with that of SiCfoam/EP. SEM images of the eroded surfaces of all composites were taken to investigate the erosion mechanism. Severe breaking of SiCp II particles was observed in SiCfoam/SiCII/EP, and plenty of SiCpIII particles were detached from the epoxy matrix in SiCfoam/SiCIII/EP (Figure 3). Nevertheless, the SiC particles in the hybrid composites were less seriously damaged than those in SiCp/EP, which can be attributed to the shadowing effect of the SiC foams. The shadowing effect decreases the impact energy of quartz sand on SiC particles. Quartz sand with small grain sizes selectively scoops out the epoxy matrix in particle-reinforced, epoxy‐based composites [15]. However, no scooping of the epoxy resin was observed in the hybrid composites because of the synergistic effect of the SiC foam and SiC particles. Therefore, the hybrid composites eroded to a lesser extent than SiCfoam/EP. The SiC foam and SiC particles greatly improved the anti‐erosive properties of the epoxy matrix, indicating that SiCfoam/SiC/EP composites behave completely different from traditional particle‐/fiber‐reinforced polymer composites under solid particle erosion conditions.
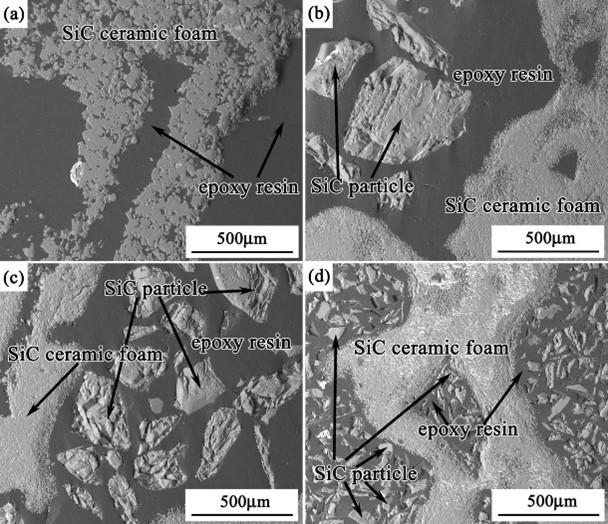
Figure 4 shows sketches of the slurry erosion mechanism for the four composites. During slurry erosion, local removal of EP from the impacted surface of the sample results in the exposure and extrusion of the SiC foam and SiC particles. After 24 h, the angle (α) between the damaged and initial surface of the SiCfoam/EP composite approximately reflects the impact angle of quartz sand (Figure 4a). Less EP is eroded and complex surface morphologies are formed during the slurry erosion of hybrid composites because of the synergistic effect of the SiC foam and SiC particles. The severe breaking of SiCp II and detachment of SiCp III occur with successive impact of quartz sand, which inevitably leads to further erosion of the EP after the removal of SiC particles (Figure 4b). The erosion of a material depends on the energy exchange between the erodent particle and the impacted material surface. When the particles striking against the target are softer than the target material, fractures (due to individual impacts) and plastic indentation may not occur [9]. Since quartz sand is softer than SiC, the plastic deformation of SiC is negligible during the collision of quartz sand with the sample surface. This means that most of the kinetic energy is transformed into rebounding energy while the rest dissipates through stress wave propagation.
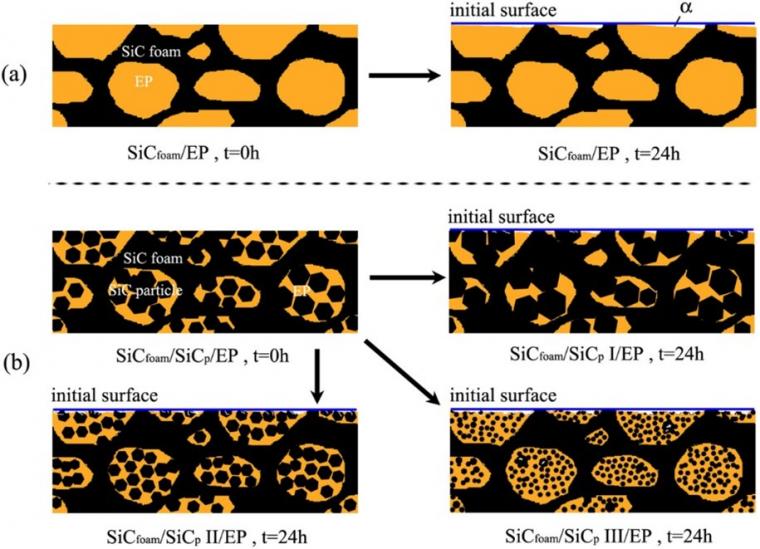
Because of its unique structure, SiCfoam dissipates the impact energy of moving quartz sand, whereas SiC particles absorb and dissipate the kinetic energy to the surrounding epoxy resin. Therefore, quartz sand with enough impact energy will inevitably break SiC particles (Figure 3c). The contact area and consequently adhesion between SiC particles and EP increase with SiC particle size. Therefore, SiCfoam/SiCpI/EP exhibited the best anti‐erosive properties, without detachment of SiCp I particles. In contrast, because of the weak adhesion in SiCfoam/SiCpIII/EP, the impact energy of moving quartz sand was high enough to detach SiCpIII particles from the composite. Consequently, SiCfoam/SiCpIII/EP showed weaker erosion resistance than the other two hybrid composites.
Conclusion
A novel hybrid composite, SiCfoam/SiCp/EP, was successfully prepared. The four composites SiCfoam/EP, SiCfoam/SiCpI/EP, SiCfoam/SiCpII/EP, and SiCfoam/SiCpIII/EP exhibited better mechanical properties than the SiCfoam/EP composite because of the reinforcement of the epoxy resin with SiC particles. The grain size of SiC particles had a marked effect on the mechanical properties of the SiCfoam/SiCp/EP composites, which increased with decreasing particle size. The SiCfoam/SiCp/EP composites also had better anti‐erosive properties than the SiCfoam/EP composite. Among the tested hybrid composites, SiCfoam/SiCpIII/EP exhibited the highest erosion rate, leading to the detachment of SiCpIII particles from the epoxy resin. The SiCfoam/SiCp/EP hybrid composite can be applied under solid particle erosion conditions because of its excellent mechanical and anti-erosive properties.
References
[1] A. Patnaik, A. Satapathy, N. Chand, N.M. Barkoula, S. Biswas, Wear 2010, 268, 1.
[2] U. S. Tewari, A.P. Harsha, A. M. Hager, K. Friedrich, Compos. Sci. Technol. 2003, 63, 3.
[3] N. M. Barkoula, J. Karger‐Kocsis, Wear 2002, 252, 1.
[4] A. P. Harsha, A. A. Thakre, Wear 2007, 262, 7.
[5] N. M. Barkoula, J. Karger‐Kocsis, J. Reinf. Plast. Compos. 2002, 21, 15.
[6] P. R. Pati, A. Satapathy, Adv. Polym. Technol. 2015, 34, 4.
[7] P. R. Pati, A. Satapathy, Polym. Adv. Technol. 2015, 26, 2.
[8] L. Z. Zhao, M. J. Zhao, X. M. Cao, C. Tian, W. P. Hu, J. S. Zhang, Compos. Sci. Technol. 2007, 67, 15.
[9] J. Liu, J. Binner, R. Higginson, Wear 2012, 276, 94.
[10] H. W. Xing, X. M. Cao, W. P. Hu, L. Z. Zhao, J. S. Zhang, Mater. Lett. 2005, 59, 12.
[11] Z. H. Ren, P. Jin, X. M. Cao, Y. G. Zheng, J. S. Zhang, Compos. Sci. Technol. 2015, 107, 129.
[12] A. C. Loos, G. S. Springer, J. Compos. Mater. 1983, 17, 2.
[13] I. Yamamoto, T. Higashihara, T. Kobayashi, Jsme Int. J. Ser. 2003, 46, 2.
[14] S. Y. Fu, X. Q. Feng, B. Lauke, Y. W. Mai, Compos. Part B‐Eng. 2008, 39, 6.
[15] S. Z. Luo, Y. G. Zheng, J. Li, W. Ke, Wear 2001, 249, 8.
[16] I. Hussainova, J. Kubarsepp, I. Shcheglov, Tribol. Int. 1999, 32, 6.
This text is a digest version of the following article:
Ren, Z., Zheng, Y., Jiang, C., Cao, X., Jin, P. and Zhang, J. (2018), Mechanical properties and slurry erosion resistance of a hybrid composite SiC foam/SiC particles/EP. Polym. Compos., 39: 2277-2286. https://doi.org/10.1002/pc.24205
Source: Preview Image: ThomasVogel/Getty Images