Stereolithography of SiOC Polymer‐Derived Ceramics Filled with SiC Micronwhiskers
Due to complicated manufacturing methods and lack of machinability, the use of engineering ceramics is limited by the manufacturing processes used to fabricate parts with intricate geometries. The 3D printing of polymers that can be pyrolyzed into functional ceramics has recently been used to significantly expand the range of geometries that can be manufactured, but large shrinkage during pyrolysis has the potential to lead to cracking. In this work, a method to additively manufacture particle‐reinforced ceramic matrix composites is described. Specifically, stereolithography is used to crosslink a resin comprised of acrylate and vinyl‐functionalized siloxane oligomers with dispersed SiC whiskers. Printed ceramic porous structures, gears, and components for turbine blades are demonstrated. [...]
Please register below to read the full article digest.
Introduction
While additive manufacturing (a.k.a. 3D printing) is readily used to fabricate various metallic and polymeric materials, fabrication with ceramics is inherently difficult. Methods currently used to 3D print ceramics most often rely upon a sacrificial polymer resin with suspended ceramic particulates; printed parts are subsequently sintered at high temperatures where the ceramic particles permanently sinter together or laser sintered. These structures are plagued by porosity which is not often uniform or well‐controlled. Consequently, mechanical properties for structural uses are lacking, which severely limits potential applications.
Recently, a handful of emerging studies have explored the use of polymer‐derived ceramics (PDCs) in conjunction with stereolithography. PDCs are a class of ceramics which have been pyrolyzed from a pre‐ceramic polymer at high temperature (e.g., see recent reviews). Specific PDCs can be tailored to exhibit functional properties such as: electrical conductivity,piezo‐resistivity and chemical resistance, among others. Via 3D printing, PDCs can be printed into complex forms where their functional properties may be used for a wide range of applications. One benefit of using 3D printing PDCs is that resulting ceramics have been described as “fully dense” or lacking any porosity in contrast the structures of more standard sintered 3D printed ceramics without any additional processing can possess porosities near 65%. While 3D printing of PDCs results in final ceramics without obvious porosity, other methods of 3D printing ceramics have also lead to final materials with high density fractions, such as 3D printing via direct ink writing. However, PDCs still undergo large shrinkage during pyrolysis, which can lead to cracking.
Particle‐reinforced PDCs undergo reduced shrinkage and cracking of the final ceramic material during pyrolysis, as compared to unreinforced PDCs. Furthermore, particle reinforced PDCs can be formulated to tailor creep‐resistance, corrosion resistance, and mechanical properties. If ceramic matrix composites resulting from pyrolysis of particle reinforced PDCs could be processed using 3D printing, the properties of the printed final ceramic could be tuned to yield increased strength, electrical conductivity, heat insulation, etc. − and be tailored to fit application needs. Since the addition of reinforcement hinders the initial polymerization process care must be taken to ensure that any additive to the resin will still be able to be 3D printed and will not cause under‐polymerization and loss of printing resolution. To date, no study has investigated the addition of ceramic particle reinforced preceramic polymer composites for 3D printing via SLA printing.
The purpose of this study was to derive a preceramic polymer system for use as a 3D printing resin that would result in a high‐quality polymer‐derived ceramic reinforced with SiC micronwhiskers. Using a siloxane precursor and the addition of reinforcement in 3D printing
resin, a 3D printable SiOC–SiC whisker ceramic was fabricated and characterized. The resulting 3D printed samples were formed into ceramics via pyrolysis and characterized through a combination of thermogravimetric analysis (TGA), Fourier‐transform infrared spectroscopy (FTIR), UV absorption spectroscopy, X‐ray diffraction (XRD), and electron microscopy. SiOC materials can be utilized in processes requiring a high‐temperature reaction catalyst, pressure sensors, and as anodes in Li batteries. Pairing SiOC with a SiC filler can help reduce cracking, shrinkage, and improve the ceramic yield after pyrolysis.
Methods
Resin Formulation: The resin formulation consisted of an initial mixture of the VMS and PEGDA in a 1:1 ratio by mass. Following initial mixing, the photoinitiator and free radical scavenger were added at 0.3 and 0.7 wt%, respectively, and mixed for another 30 min at 1000 rpm. For resins containing SiC whiskers, the particles were added at 0.5 wt% corresponding to 1.45% volume fraction as determined by the densities and weight fractions of the materials; the mixture was again mixed at 1000 rpm for 30 min resulting in a well‐dispersed mixture as observed visually.
Reinforcement Characterization: The SiC whisker reinforcement size and geometry was investigated by laser scanning confocal microscopy (LSCM). Images were captured with an Olympus OLS 4000 LEXT LSCM (Olympus Corporation, Tokyo, Japan) capable of 3D measurements with 10 nm height resolution and 25 nm x‐y resolution. Quantitative analyses of SiC diameter and length‐to‐diameter ratios were measured using the Olympus software. The as‐received SiC whiskers were also characterized by XRD.
Stereolithography: Preceramic polymer resins were 3D printed using a FormLabs Form 1+ stereolithographic (SLA) printer, where polymers are photo‐cured using a 405 nm wavelength laser. After printing, parts were cleaned using isopropanol to remove the residual uncured resin on the surface and subsequently post‐cured under a 20 W UV lamp (Quans High Power UV LED light) with a wavelength of 405 nm for 20 min.
Results
Fabrication of the base resin was made up of four constituents: an −ene containing monomer with an average of six functional groups (poly(vinylmethoxysiloxane) or VMS), a monomer with 2 acrylate functional groups (Poly(ethyleneglycol)‐diacrylate or PEGDA), as well as comparatively small amounts of photoinitiator (Irgacure® 819), and free radical scavenger (Irganox 1330™) needed for photopolymerization during 3D printing.35 The two monomers, VMS and PEGDA mix very well when shaken into a translucent mixture by hand as the density and viscosity of both oligomers are very similar. The free‐radical scavenger and photoinitiator were both soluble in the monomer solution and straightforward to mix. Through a systematic study varying both the free‐radical scavenger and photoinitiator, the final resin formulation utilized a ratio of free‐radical scavenger to photoinitiator ratio of 3:7 by weight; this ratio resulted in the most distinct features for the 3D printed structures.
SiC whiskers were selected as a filler as they would have no complex interaction with the PDC matrix and have been previously investigated in traditional composite PDCs.15 XRD (Figure 1a) and laser scanning confocal microscopy (LSCM) measurement of SiC whiskers confirmed material and manufacturer dimension specifications, with whiskers approximately 2 μm in diameter and having a length‐to‐diameter aspect ratio of roughly 20 (Figure 1b). Most of the whiskers are relatively straight; however, several were observed to have curling or spiraled geometries while remaining intact. With the addition of 0.5 wt% SiC whiskers into the base resin, no apparent changes in the viscosity nor the strength of the polymerized part were identified. The SiC whiskers maintained suspension in the mixture for up to 12 h before naturally settling. For all results shown here, printing was performed within1 h of mixing
Figure 1
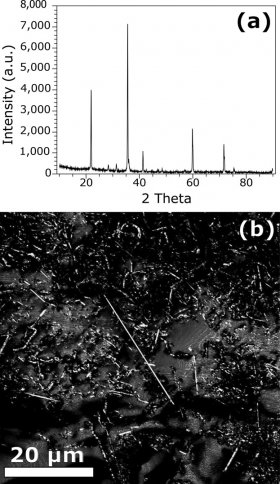
XRD of the SiC whiskers used as reinforcement a) and laser scanning confocal microscopy inensity image of the SiC whiskers where the dimensions of SiC whiskers can be measured b).
A key parameter in stereolithography is the selection of the energy used to cure the resin. Through FTIR, the chemical functional groups' reactions and structural changes of the polymer system were observed for two different UV exposure times of polymerization process in the base resin.
Comparing FTIR results of VMS‐PEGDA with and without SiC whiskers (Figure 2d), C═C bonds from both the vinyl group and acrylate functional groups exhibited smaller normalized peak intensity in the base resin than those in with SiC whisker reinforcement, indicating the presence of SiC whiskers inhibited crosslinking during the polymerization process.
The 3D printing of both materials was successful; however, when printing the base resin, there were some areas of over‐polymerization, especially on the edges of the print with some areas containing what looked like cured droplets jutting off of the features. When comparing the printing process, it was noted that the resin with the inclusion of SiC whiskers tended to result in more defined structures with little areas of over‐polymerization (Figure 3). As such, the SiC reinforced resin was preferred for most 3D printed parts.
Figure 3
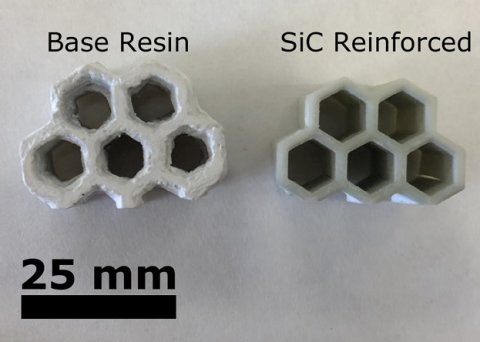
Comparison of the x‐y resolution of the base resin and resin reinforced with 0.5 wt% SiC whiskers printed using identical initial designs and printer settings. The filled resin results in a significantly less over‐polymerized sample and is more defined in the x‐y plane.
To understand the polymer to ceramic conversion process of the pre‐ceramic polymer, a sample of 10 mg of material was pyrolyzed in a TGA in an argon atmosphere where the change in mass and heat flow measurements were analyzed over the course of the pyrolysis process (Figure 5). Initial testing was performed to identify discontinuities in mass or heat flow which indicates that the material was undergoing chemical change (e.g., side groups of the polymer outgassing). Based on these measurements, the temperatures at which these phenomena occurred were held at isothermal dwell times to ensure the whole system came to equilibrium. The explicit purpose was to allow any reaction occurring to complete before further heating. The mass loss and heat flow are shown in Figure 5, and the temperature profile utilized in pyrolysis was determined via the TGA results. When initially heated from room temperature there is a steady mass loss beginning at 350 °C terminating at about 500 °C. Within this temperature range, the pre‐ceramic polymer fabricated with the base resin loses 63.1% of its initial mass whereas the resin reinforced with SiC whiskers only loses 61.6% of the initial mass. During preliminary investigations, there was a heat flow dip at both 500 and 725 °C. Here, this is represented by in the severe drops in Figure 6 where the TGA temperature was held isothermally. In the case of the heat flow change at 500 °C, corresponding to the material's transformation to an inorganic material. At 725 °C, there is again a change in heat flow associated with the formation of amorphous SiOC. Not only does the mass loss change with the addition of SiC whiskers but the heat flow at higher temperatures is reduced slightly as the changing matrix is mixed with stable SiC whiskers.
Figure 6
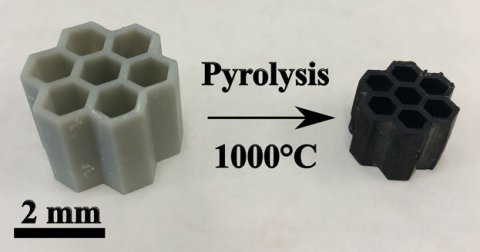
Image of 3D printed pre‐ceramic polymer and subsequent pyrolyzed material at 1000 °C ceramic using the base resin.
After the pyrolysis process, the polymer derived ceramic sample is measured to calculate shrinkage and ceramic yield. The base resin resulted in an average isotropic shrinkage and ceramic yield of 43.1 ± 0.38% and 36.9 ± 0.31%, respectively, over a study of 10 samples and in all three directions for shrinkage measurements. Initially, shrinkage was measured in three perpendicular directions, however, percent shrinkage was noted to be isotropic and directional shrinkage values were averaged. With SiC reinforcement, the shrinkage and ceramic yield are both impacted with a decrease in shrinkage to 37.2 ± 0.38% and an increase in ceramic yield to 38.4 ± 0.26%, similar to the increased in retained mass noted in the TGA results. With or without further processing the 3D printed PDC may be used for such as small scale turbine blades or applications requiring high surface area to volume ratios. Several scale models of ceramic 3D printed geometries made from this process can be seen in Figure 7. The three larger turbine blades are manufactured from pyrolysis of the base resin, where surface cracking of the polymer during post‐curing was a minor problem. The remainder of these samples are manufactured from the SiC reinforced resins with 10 μm resolution. Of particular interest are the wheel hub (far left) which has 3D printed threads such that the appropriate axel can be attached, demonstrating the ability to create machinery elements, and the inverse FCC structure which demonstrates the scales of accomplishable porosity using this 3D printed methodology. However, it should be noted that this is not the finest resolution possible
Discussion
The addition of SiC particles into polymer derived ceramics has been shown to mitigate both mass and shrinkage in addition to aiding to reduce cracking.11 Therefore, 3D printing a polymer‐derived ceramic reinforced with SiC whiskers was investigated. SiC was chosen as the reinforcement due to its high‐temperature stability.36-38 Through this process, research goals of reducing shrinkage and mass loss were achieved. In addition, the whiskers added a degree of absorption which aided in overall printing definition. This was accomplished by using the resin described in a constituent ratio where VMS would be the limiting factor as the acrylate side groups more readily reacts with itself.39, 40 From a 1:1 molar basis, the ratio of the monomers would result in weight ratio between VMS to PEDGA as 1.39:1. As VMS is a silicon‐backbone containing polymer, it is anticipated that this ratio would produce a material with higher ceramic yield corresponding to the higher composition of Si in the system. Despite this, with the reaction rate of the PEGDA, it is anticipated that the there is a higher relative concentration of acrylates bonding to other acrylates than the vinyl group. However, as many photopolymer 3D printing resins are acrylate‐based, the rate of reaction may aid with the printing process as a whole.
Varying ratios of free‐radical scavenger and photoinitiators, the optimal ratio was found through a tailored systematic study which reduced over‐polymerization by increasing the free‐radical scavenger − which aided in localizing the reaction. However, a balance of photoinitiator was required to ensure polymerization occurred and sufficient polymerization depths during 3D printing could be achieved. From SLA printing theory, there must be a small layer of under‐polymerized material at the outer edge of each layer such that the next layer can easily bond35 and with increasing exposure time this thickness of the unpolymerized material is minimalized. As the settings in the printer are present and involved to determine independently, the resin formulation needed to be experimentally derived to ensure proper printing definitions utilizing the given pre‐defined constraints of the 3D printer: exposure time, laser intensity, and laser speeds. As noted in the FTIR results, a minor increase in exposure time decreases the peaks of the C═C bonds found in the VMS functional groups (Figure 2b), indicating an increased degree of crosslinking. As such, determining the photoinitiator and free‐radical scavenger ratio was an iterative process. The process of adjusting the ratio of these two essential chemicals was repeated until a clear structure could be printed.
Within the context of the photoinitiator, the concentration cannot be too high or the prescribed exposure times by the printer would initiate a nearly full polymerization leading to several issues. The next layer could potentially not adhere to the previous leading to a premature print failure or over‐polymerization − causing ill‐defined polymerization in the x‐y dimensions of the printer − would occur effecting print resolution. In the case of the VMS‐PEGDA reaction, a ratio of 0.3 to 0.7 wt% (free‐radical scavenger: photoinitiator) was determined to be optimal through these parameters and utilized for 3D printing. However, the x‐y resolution of the samples was not optimized with the photoinitiator to free‐radical scavenger ratio alone and was further aided by the addition of the SiC reinforcement. Figure 3 displays the degree of over‐polymerization in the base resin which is mitigated by the addition of SiC in the filled resin, where there is little over‐polymerization when printed with identical settings. This is likely due to the printer setting being better suited to the penetration depth of the SiC resin, using an SLA printer with adjustable settings, the over‐polymerization in the base resin could be mitigated further. This is typically achieved by determining a working curve of penetration depth as a function of increasing energy dose,35, 41 however with limited settings on the 3D printer to be adjusted, such a study could not be related to the printing system.
Except for the definite decrease in the C═C bonds in the vinyl functional group with both increase in exposure time and the addition of the SiC whiskers, there was little change in the bonds found in the backbone of the Si‐containing polymer. This indicates that increase in exposure time and, therefore, crosslinking did not have an effect on the bonds that influence pyrolysis. In the case of the reinforcement addition, crosslinking is inhibited due to the physical blocking of light during the polymerization process. Despite the necessity for lower general crosslinking needed for proper 3D printing, highly crosslinked pre‐ceramic polymers result in less cracked or warped PDCs.42-44
This effect serves the same general function as a UV absorber where the purpose of UV absorbers used in SLA 3D printers has been to hinder polymerization depth.47 Using a reinforced resin did not lead to any adverse interactions during polymerization or of the resultant polymer. These results indicate that SiC particles may act as suitable replacements for chemical UV absorbers in certain 3D printing resins. The function of many of these chemicals is to absorb the UV radiation preferentially to all other constituents and dissipate the energy as low‐level heat,48 hindering the formation of free radicals by reducing UV contact with the photoinitiator. In contrast, the SiC whiskers − which have yet to be used in SLA printing of PDCs − block the passage of UV, inhibiting polymerization.49 The addition of solid particles in SLA printing has been of particular research interest in the field of polymer matrix composite fabrication.50 Despite the decrease in crosslinking of the reinforced resin (Figure 2d), the introduction of ceramic particles into PDCs has been found to reduce the effect of necessary cross‐linking in the pre‐ceramic for the polymer to retain its shape − as the particles maintain shape and hinder the flow of the softened polymer during pyrolysis.51, 52
The results of the TGA are as expected compared to several other studies of siloxane pyrolysis.53-56 The initial mass loss can be attributed to the removal of much of the PEGDA side groups, in particular, the numerous oxygens found in the backbone, contributing to much of the mass loss. Concurrently, removal of some hydrocarbons also occurs (specifically CH457) and likely reorganization of the Si–O, Si–C, and Si–H bonds through various reactions58 − contributing to the change in heat flow. Beyond the initial stages, the heat flow change at 725 °C is attributed to cleavage processes of C–H, Si–O, and Si–C bonds as the material transforms to an amorphous SiOC with residual free carbon.57 During this stage dissociation of cleaving Si–C and C‐H bonds results in the removal of additional CH4 and H2 from the system.
The XRD of the ceramics agrees with literature in that the resulting SiOC is amorphous. Comparing fabrication of typical SiOC at temperatures around 1000 °C, it is well established that this material should be amorphous.59 XRD plots of the base and SiC reinforced resins look nearly identical. Some trace of SiC peaks might be expected within the ceramics that are reinforced with the whiskers. However, at 1.45% volume fraction of the whiskers to the matrix of the ceramics, it is likely that the SiC peaks are on the same order as the noise in the data and, therefore, cannot be detected. It is clear from the SEM that the SiC whiskers remain intact and separate from the ceramic matrix and are unharmed during pyrolysis. Therefore, not only do reinforcements added to 3D printing resins affect print absorbance and quality but in the printing of preceramic polymers, these reinforcements can be used to impact the shrinkage and properties of the final ceramic, both of which may be beneficial to future applications.
The reduction in shrinkage is as expected with the SiC reinforcement hindering shrinkage during pyrolysis. With the notable exception of shrinkage in the material, ceramics made from the base resin or those with SiC whiskers appear nearly identical. As the shrinkage was uniform in all three dimensions, these ceramics look like scaled models of their preceramic stage with no discernible difference in shape retention and no cracking from internal stresses of dimension mismatch during pyrolysis. Upon SEM investigation, it is noted that there was no apparent porosity nor cracking throughout the entire resulting ceramic. With relatively small or few pores, this makes the ceramic stronger and more resistant to fracture as ceramics are inherently flaw dependent with pores often acting as nucleation sites for failure. As the resulting ceramic made from the base resin shows no obvious cracking throughout, it is not possible to confirm that the SiC reinforcement aided in crack reduction during pyrolysis despite the fact that ceramic reinforcements in PDCs have been proven to have this effect.60 Furthermore, the inclusion of the SiC whisker reinforcement appears to have a relatively strong bond with the ceramic matrix as the whiskers do not seem to pull out upon fracture of the final ceramic, indicating that the SiC whiskers are separate entities within the ceramic.
Despite the apparent lack of porosity in the final ceramics, there must be a small degree of undetectable voids or cracking. The density of the SiOC reinforced with SiC whiskers drops slightly from 2.99 to 2.86 g cm−3. This drop in density can account for the large decrease in shrinkage with only marginal amounts of SiC whiskers added initially. Regardless of the drop in density, mechanical properties of the reinforced ceramic still improves well beyond the standard deviation of the measured hardness values of the SiOC. The hardness values of SiOC materials has been previously determined to be in the regime of what was calculated for the final ceramics in the present study55 and as such are as expected.
Conclusion
Throughout the study, a siloxane‐based pre‐ceramic polymer and the resulting pyrolyzed SiOC fabricated via stereolithography 3D printing created both a SiOC polymer‐derived ceramic and SiOC–SiC ceramic matrix composite which was characterized. The photopolymerizable resin was comprised of a vinylmethoxysiloxane homopolymer and poly(ethyleneglycol)‐diacrylate and was studied with and without the addition of SiC whiskers as a reinforcement. The UV absorbance of the resin with SiC whiskers added was increased by an order of magnitude when compared to the base resin. Additionally, the definition of 3D printed samples was increased in the presence of SiC reinforcement. Both the base polymer and polymer matrix composite's pyrolysis behavior were analyzed via TGA and subsequently shown to be an amorphous SiOC ceramic via XRD. Not only did the SiC whiskers act as a de facto UV absorber during photopolymerization, but also hindered shrinkage to an average of 37.2% from the base resin's 43.1% shrinkage after pyrolysis. The final ceramic yields were measured to be, on average, 36.9% and 38.4% for the base resin and those which used SiC reinforcement, respectively. Investigating the SiOC 3D printed ceramics via microscopy, there was no obvious porosity or cracking within the structures, and SiC whiskers are clearly embedded in the SiOC matrix.
Source: Preview Image: Marina Skoropadskaya/Getty Images